We may earn revenue from the products available on this page and participate in affiliate programs. Learn More ›
Radiant floor heating is arguably the ideal home heating system. It’s comfortable, efficient, unobtrusive, quiet, and does not blow dust and allergens around the way forced hot air systems do. Instead of overheating the room’s perimeter in the hopes that the warm air will travel throughout the space before rising, subfloor heating serves up heat from below. The result is a more even overall heat that warms everything in the room, including surfaces, furnishings, and, most importantly, you. Radiant heat is similar to the heat you feel when you stand by a window on a sunny cold day. Your face feels warm, but the sun didn’t need to heat the air outside to make you feel that way.
For the record, subfloor heating has been around for centuries, from the hypocausts—a floor raised on pillars where heat could circulate below and radiate through layers of tiles and stone—of the ancient Turkish and Roman baths, to Frank Lloyd Wright’s turn-of-the-century adoption of more modern Japanese examples. And while the decision to install radiant heating used to be a pre-construction call, today’s innovations make it feasible—and, even DIY-suitable—for existing home retrofits.
Types of Radiant Floor Heating Systems
Radiant floors are heated either with electric resistance cables or hot water flowing inside tubing.
Electric systems
Electric radiant heating systems are typically supplemental, not meant to be the sole heat source for a room. The cables, which are often pre-attached to mats for ease of installation, are installed over the subfloor in a bed of thin-set mortar. Ceramic or stone tile are popular finished floor choices. There are also radiant electric floor heating pads that can be installed under laminate and other floating floors, such as engineered hardwood. One manufacturer, Thermosoft, makes pads that produce 31 BTUs per square foot. Installation is simple. Just roll it out, tape it in place, cover with floating-type flooring, and make the electrical connections. No mortar is required.
Don’t want to pull up your existing flooring? Companies such as SunTouch make electric radiant pads that fit in joist bays under the subfloor. You will, of course, need access to the bays from a basement or crawl space. Batts of fiberglass insulation are installed under the mats so most of the heat goes up, not down.
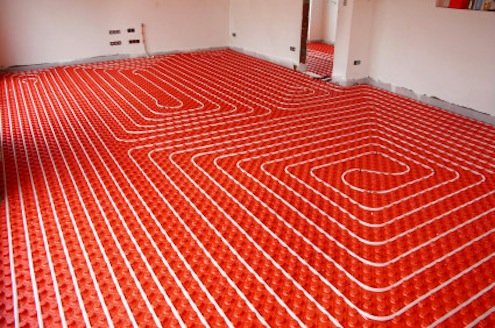
Hydronic systems
Hydronic radiant heating systems are usually designed to heat an entire house. Water is heated to between 100 and 120 degrees Fahrenheit by a boiler and circulated through tubing under floors. The tubing can be installed in several ways: embedded in a concrete slab, installed over an existing slab in cement, stapled under subflooring, or fitted inside the channels of specially designed subfloor panels. Any kind of finished flooring, including hardwood strip flooring, vinyl, or carpeting, can be installed above it. (Note: Some installers may recommend engineered wood rather than solid wood flooring products in homes with high moisture levels. Otherwise, changes in moisture content can cause wood planks to cup, bow, or warp.)
More Comfort, Lower Energy Costs
Radiant heating is more comfortable than other systems for a variety of reasons. First and foremost, it feels warmer because the heat is delivered where you live—near the floor. Since all surfaces in the room are also being heated, there are no cold objects to draw heat from you and make you feel cold. In addition, radiant heat does not constantly cycle on and off, causing you to be too hot one minute and too cool the next. Nor does it dry out the air that in turn dries out nasal membranes. Plus, radiant heat is relatively draft-free. There are no supply and return registers or convection-reliant radiators, and there is less air leakage around doors and windows. Finally, the air inside the home tends to be cleaner because dust and allergens are less likely to be stirred up by air currents.
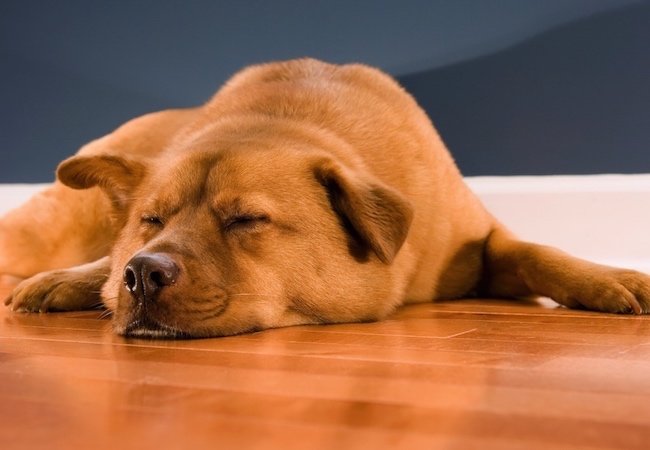
Because electric heat is expensive, electric radiant floors are typically limited to small areas, such as a bath or kitchen. Programmable thermostats with both air and floor temperature limits are recommended with such systems, to save on energy costs. Hydronic radiant floor systems save energy and lower fuel bills because radiant heat feels comfortable at lower air temperatures, enabling you to lower the thermostat. Further savings can be realized because running a high-efficiency boiler at lower temperatures will increase its lifespan. In addition, hydronic radiant heat is more efficient than other systems because it uses relatively low water temperatures to heat your home. In effect, the entire floor is a radiator, so it doesn’t have to be as hot as conventional radiators. Boilers can heat water to lower temperatures more efficiently than they can heat water to higher temperatures.
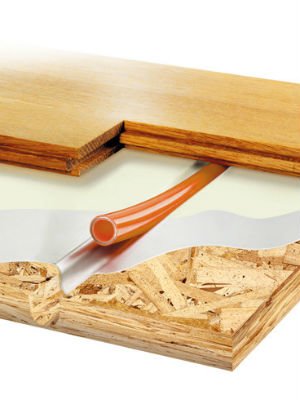
Recent Innovations
The growing popularity of PEX (cross-linked polyethylene) tubing during the past 15 to 20 years has made radiant floors easier to install and leak-free. This was not so with ‘50s- and ‘60s-vintage radiant systems that relied on copper tubing embedded in concrete. With time, the tubing leaked and the systems were abandoned. Early on, PEX was not without hiccups as well. Tiny amounts of oxygen are able to penetrate the PEX lining, causing corrosion to metal components, such as cast iron boilers. Newer versions of PEX include an oxygen barrier.
The growing popularity of solar heating has also caused builders and homeowners to give radiant floor heat a second look. Solar energy is a good heat source for radiant floors because solar thermal collectors are very efficient at supplying the lower water temperatures that such systems require.
Simplified installation
Installations have been simplified in recent years with the advent of subflooring that’s pre-fitted with tubing channels. Warmboard, for example, manufactures 4 x 8 radiant floor panels for new construction and 2 x 4 panels for remodeling that are lined with aluminum sheeting for even heat distribution. The panels are more expensive than materials used in some other systems, but they are more efficient and reduce the labor costs, too.
Radiant cooling
The only negative for radiant floor heating is that it’s not so easy to use for cooling. With a conventional forced-air heating system, the same ducts that deliver hot air through ducts from the furnace can be used to introduce cool air from a central air conditioner. While radiant cooling is possible, it’s typically not cost effective to install. A chiller or geothermal heat pump must be used to supply the cold water. In addition, the tubing for radiant cooling is best run in the ceiling (not the floor, the better location for heating). And while radiant cooling systems will reduce air temperature, dehumidification may also be needed to make occupants feel cool.
Costs of Radiant Floor Systems
For new construction, a hydronic radiant floor system is likely to cost more than forced hot air (ducts and registers) or hydronic systems (baseboard radiators). In the long run, however, it will save money due to lower thermostat settings and higher efficiency. The cost of retrofitting hydronic radiant flooring varies depending upon whether there is access to the subfloor and the extent to which flooring and ceilings must be torn out and reinstalled. As a starting point, materials and mechanical equipment for installing hydronic radiant heat in a 2000 sq. ft. home cost about $3,500 or $1.75 per sq. ft., according to the Radiant Floor Company. This excludes the heat source and assumes two zones (a 1000 sq. ft. basement and 1000 sq. ft. first floor). Labor costs vary by the job and location.
Electric radiant floor heating costs about $6 per sq. ft. for materials but is often less expensive to install because of lower labor costs. Unfortunately, it’s far more costly to operate and therefore generally makes sense as a supplemental, not primary, heat source.
Is Radiant Heating Right for You?
Radiant heat—a no-brainer if you’re building a new house—can be retrofitted to fit the floors of existing homes, too, although installation costs will be higher. In retrofits, tubing is attached to the underside of the first-floor subfloor, assuming there is access to it from a basement or crawl space. If the renovation is extensive and the finished floor is going to be replaced in any case, it’s usually better to install tubing over the subfloor where it will be more efficient, easier to install, and require less tubing. Adding radiant heat to second and third levels, when existing floors are to remain in place, may require removing the ceiling of the rooms below to gain access to the underside of the subfloor.
Your heat source will also factor into your decision. If you have an efficient boiler that’s not too old, it probably can be used to supply heat to your radiant floors. If your boiler has seen better days, choose a high-efficiency, condensing, gas-modulating boiler that is capable of heating your domestic hot water, too.