We may earn revenue from the products available on this page and participate in affiliate programs. Learn More ›
Highlights
- Foundation cost typically ranges from $5,200 to $148,000, but the national average is $9,100.
- The type and size of foundation, type of structure, permits, soil testing, prep work, and labor rates are some of the main factors for calculating the cost of a concrete foundation.
- Concrete foundations provide a stable base for a structure to sit on and withstand extreme weather conditions. They can also provide energy savings when they are insulated and waterproofed.
- Pouring a foundation requires expertise, special equipment, and a knowledge of structural support calculations, so it’s a job best left to a professional concrete company or general contractor.
A home’s foundation is often hidden from sight, but that doesn’t negate how absolutely vital it is for the strength, stability, and health of the structure it supports. Since a foundation is so crucial to a solid house, it’s not a component that can be overlooked or rushed during the design or construction process. It’s an essential piece of the project, and so homeowners are often curious about foundation costs.
There’s no one-size-fits-all price when it comes to the cost of a foundation. According to Angi, the national average foundation cost is $9,100, though a typical range is $5,200 to $148,000. There are several factors homeowners should consider when estimating their foundation’s total cost.
For instance, soil type can determine the type of foundation required for the building, significantly influencing costs. Foundation size, regional labor rates, and site-specific challenges also play a role in estimating how much it will cost to build a foundation.
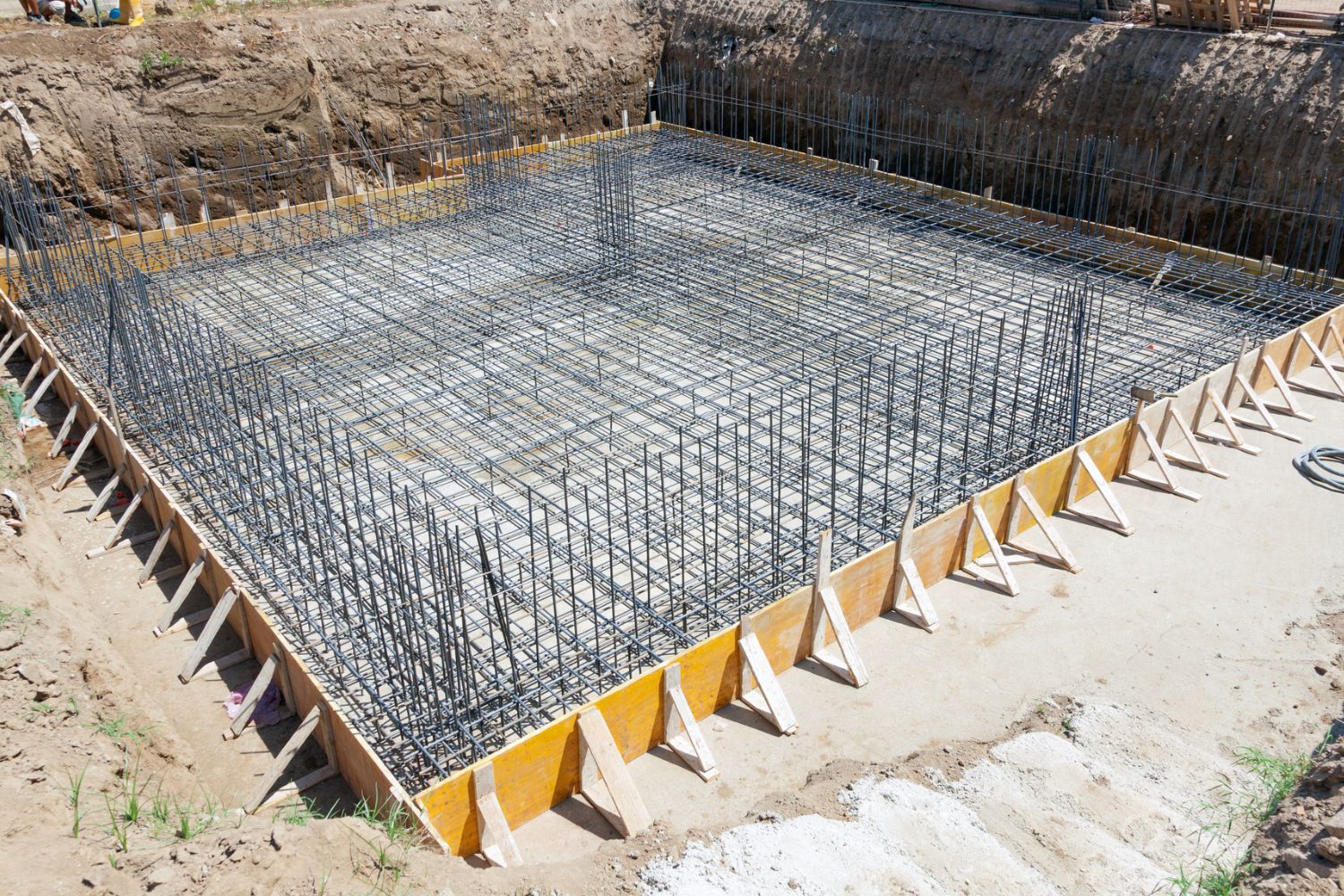
Factors in Calculating Foundation Cost
Foundation costs can be complex, and while the national average offers a general benchmark, it’s often just the tip of the iceberg. Knowing the most influential aspects that affect concrete foundation costs can help homeowners plan their budget accordingly.
Foundation Size
Foundation projects are usually charged based on square footage. Generally, larger foundation footings cost more to lay, while smaller foundations are more cost-effective. The average foundation cost per square foot is between $5 and $37, so homeowners can expect the foundation cost for 1,000 square feet to fall anywhere between $5,000 and $37,000.
Besides size, there are a few related factors for readers to keep in mind. For example, depth, complexity, soil preparation needs, and local labor and material rates can all play a role in determining a foundation’s cost in relation to its size. So, a small but deep basement foundation in a highly populated area may cost more than a large slab foundation in a rural location.
Foundation Size | Average Cost Range (Materials and Labor) |
500 square feet | $2,500 to $18,500 |
1,000 square feet | $5,000 to $37,000 |
1,500 square feet | $7,500 to $55,500 |
2,000 square feet | $10,000 to $74,000 |
3,000 square feet | $15,000 to $111,000 |
Foundation Type
The type of foundation chosen for a project greatly influences the final cost. Different foundation types require different materials, construction methods, and timelines to complete, resulting in widely different cost ranges.
For example, a full basement foundation ($20 to $37 per square foot) will likely require more concrete and reinforcement than a slab-on-grade foundation ($4 to $14 per square foot). Homeowners can almost always expect the cost to pour concrete slab foundations to be more cost-effective than the cost to pour full basement foundations, while crawl space and block foundations tend to fall somewhere in the middle.
Homeowners are advised to choose a foundation type based on structural and environmental needs over price alone. While some foundation types are more affordable, they may not be appropriate for every building scenario and can result in costly repairs, potential safety issues, and premature replacement costs down the line.
Structure Type
Foundations have unique features and pricing depending on the type of structure they are supporting. Concrete slabs are a popular choice for homes and sheds. They’re typically quicker to construct and use less concrete and fewer materials. The straightforward process to lay a concrete slab often leads to lower costs.
Structures requiring a full basement foundation often need a deeper excavation, increasing labor and equipment costs. Basement foundations also use more concrete and need additional reinforcements, which can increase pricing. Waterproofing and incorporating features like windows and emergency exits can also lead to higher costs.
Garage structures often need thicker slabs or reinforced floors to support the weight of vehicles and additional storage. Incorporating electrical wiring and drainage systems can also boost costs.
Mobile homes are another structure to consider when homeowners are comparing foundation costs. Mobile homes often use pier and beam foundations, which is a more cost-effective option for this style of home. However, floating slabs, crawl spaces, and basements are other options—all of which come at their own price points.
Structure Type | Average Cost Range |
Concrete slab | $5,200 to $21,000 |
Full basement | $24,000 to $50,000 |
Garage | $2,000 to $7,000 |
Mobile home | $3,000 to $36,000 |
Footings
A foundation doesn’t always require footings. For example, a floating slab might remain stable without traditional footings depending on the expected load or soil composition. Lightweight structures, such as sheds, might not require footings beneath the foundation either. But for homes, garages, and oversize sheds or workshops, footings are needed to act as the base support and distribute the structure’s weight across a larger area of the ground.
Concrete footings cost an average of $6.50 per square foot. When the footings are priced per volume, homeowners might get an estimated cost of $150 per cubic yard. Overall, concrete footings typically add between $5,200 and $15,700 to a foundation’s total cost, with final pricing heavily dependent on the depth and width of the footings.
Labor
Constructing a foundation requires skilled workers, which comes at a cost. Concrete labor costs for installing a foundation usually represent between 40 percent and 60 percent of the total project budget. That translates to homeowners spending approximately $4,500 to $18,500 on labor alone when pouring a foundation.
Several factors influence the final labor cost of a foundation, including project duration and complexity. More complex types of foundations tend to need more working hours, which can raise labor costs. The geographic location also plays a role in the final price, since areas with a higher cost of living or limited availability of foundation labor typically charge higher rates.
Permits and Inspections
Building a foundation typically requires a permit to meet the city’s construction regulations. The foundation contractor or construction company generally handles initiating and pulling the necessary permits before beginning any work. However, homeowners are advised to confirm this process to avoid fees or penalties.
Most foundation companies roll the cost of permits into their overall quote, and homeowners can often find it as a separate line item on the quote. If paid separately, the cost of a building permit can range from $450 to $2,300 based on project size and specific requirements.
After a permit is secured, periodic inspections may be required during different phases of construction rather than only at the end of the project. Foundation inspections are necessary to ensure compliance with safety and building codes.
Soil Testing
Foundation costs are influenced by soil testing, an examination process used to determine the composition and properties of the soil where foundation construction is planned. This helps engineers and general contractors understand the strength of the soil conditions so they can determine which type of foundation is best suited or required to meet building safety codes.
Geotechnical soil tests are required for construction purposes, costing between $1,000 and $5,000. The final cost depends on the extent of the test, along with the location and accessibility of the site. While soil testing does increase construction costs, it ensures that a stable foundation is built on the ground and reduces the risk of future structural issues.
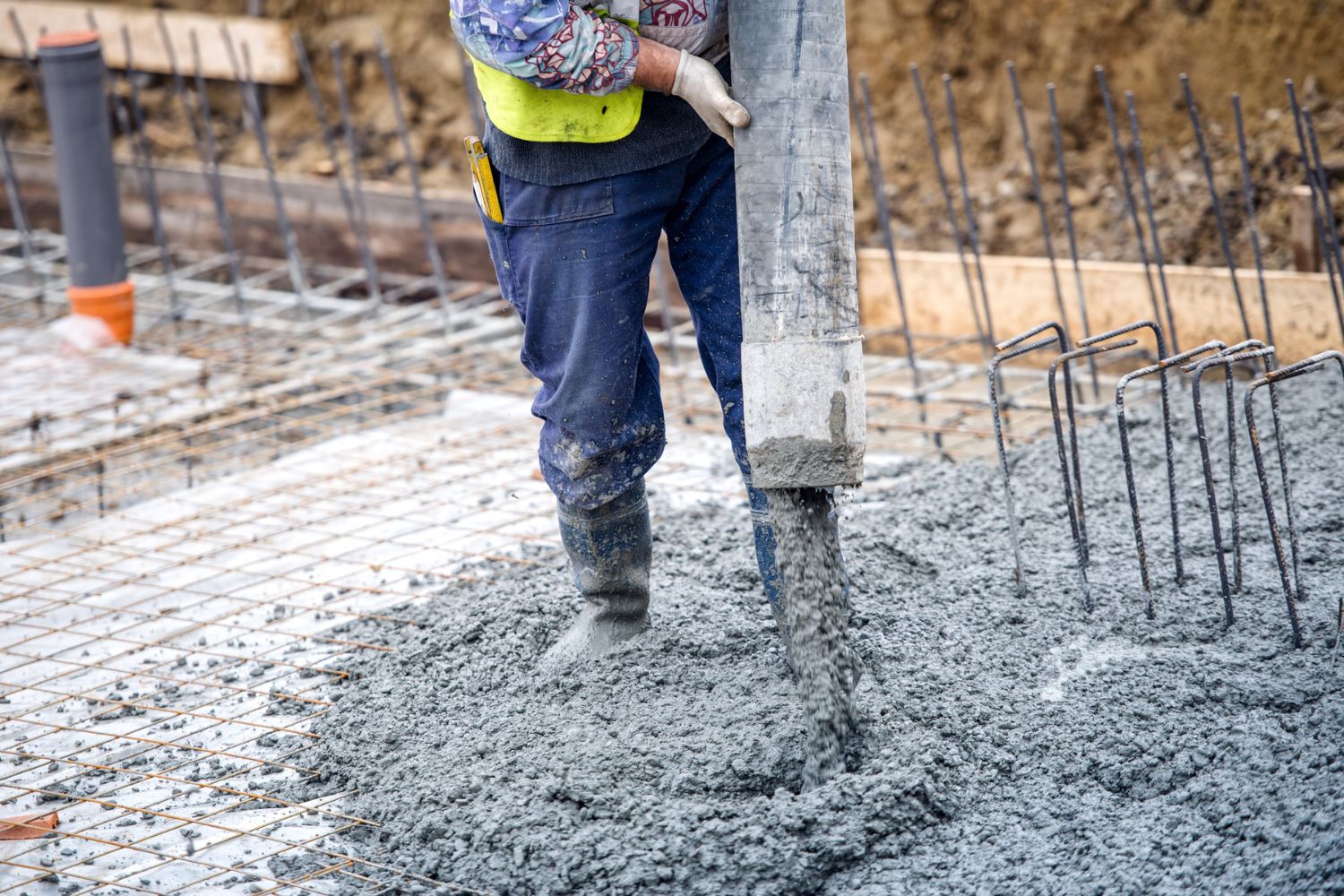
Additional Costs and Considerations
A new foundation project has several immediate costs. However, there are multiple layers for homeowners to consider when budgeting for foundation work, with several potential additional costs to keep in mind. Costly surprises are less likely to occur during the construction of a foundation when homeowners are aware of potential costs that could apply to their project.
New vs. Replacement Foundation
A major cost factor to consider is whether the project is a new foundation or a replacement. Installing a foundation for a new home typically costs between $18,000 and $30,000. The process involves testing the soil and preparing the land for foundation work before beginning work on footings or pouring concrete. Additional preparation work like tree or rock removal can raise costs.
However, a full foundation replacement ranges from $25,000 to $115,000—significantly more for several reasons. The higher costs include the demolition and removal of the existing foundation, along with the additional material and labor costs associated with adding temporary supports to hold up the structure if needed. Finally, the work to replace a foundation can unveil hidden water damage or deteriorated materials that even the best foundation repair companies (such as Basement Systems or Ram Jack) can’t address without adding unexpected costs.
Architect Fees
An architect specializes in designing and planning structures. When it comes to foundation construction, an architect can provide valuable insights for maximizing the use of the land. Every piece of land is unique in terms of slope, soil type, and climate. Having a foundation designed by a professional to best fit a site’s unique challenges and opportunities can be quite valuable.
Architect fees range from $2,000 to $10,000, depending on the project’s complexity and the architect’s experience. While working with an architect comes with an added cost, it means that a foundation will meet local building codes and offer long-term stability.
Grading and Excavation
Grading is the process of leveling land to achieve an ideal slope or elevation. Proper grading helps water drain away from the home, preventing potential water damage.
Excavation involves removing soil, rocks, or other debris from the site to create space to dig and build. Without proper excavation, a foundation might not be placed at the correct depth or on stable ground. Grading and excavation costs are often combined at an average cost of $2 to $10 per square foot.
Sealing and Drainage
Water can be a foundation’s worst enemy. Persistent water exposure can compromise a foundation’s structural integrity over time, leading to cracks, shifts, and even potential collapses.
Sealing the concrete and adding proper drainage can safeguard a foundation. Such preventive measures before damage occurs helps homeowners feel confident that a foundation will last as long as possible, minimizing expensive foundation repair costs down the line.
Sealing a foundation typically costs between $1,900 and $7,300. Adding a drainage system to redirect water away from the foundation costs between $1,100 and $6,500. Some building codes dictate if and where a drainage system is required, partly based on soil and geotechnical test results. While both are added costs for homeowners to absorb initially, the long-term savings can be monumental.
Sump Pump Installation
Sump pumps are usually installed in the lowest part of a basement or crawl space. Their purpose is to prevent water buildup by pumping out water and diverting it away from the home. Removing excess water from rain, melting snow, or rising groundwater drastically minimizes the risk of flood damage.
While sump pumps aren’t always necessary, a sump pump can safeguard the foundation and protect stored belongings in homes in flood-prone areas or those with high groundwater levels.
Homeowners can expect to pay anywhere from $650 to $2,050 for sump pump installation, depending on the pump type and complexity of installation.
Insulation Installation
Foundation insulation costs between $1 and $5 per square foot, depending on the insulation type and thickness. Installation complexity also plays a role in how much it costs to insulate a foundation.
Designed to prevent heat transfer, foundation insulation can be made from fiberglass, foam, or cellulose. Proper installation means homeowners can expect reduced energy bills and a more consistent and comfortable indoor temperature.
Insulation also helps in preventing moisture intrusion and consequential mold. In colder regions, insulation can also help to protect exposed pipes from freezing and bursting in extreme temperatures.
Not all foundations need insulation. But in colder climates or homes with foundations below ground level, insulation can be an investment that offers energy savings.
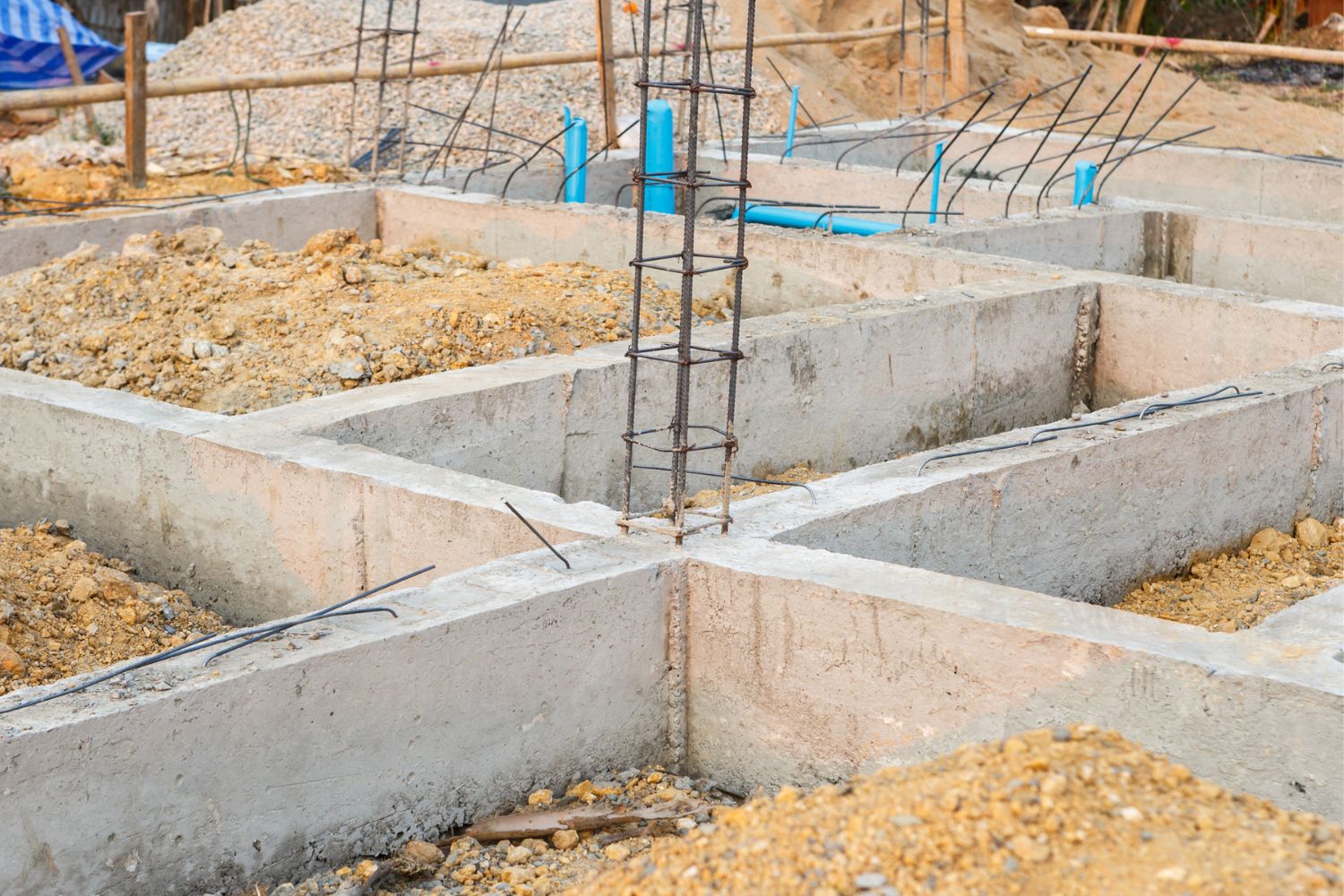
Types of Foundations
There are several types of house foundations, with each option offering unique advantages and pricing. When more than one type of foundation is suitable for a property, homeowners will want to consider the pros and cons, average costs, and suitability of each type before making a decision.
Type of Foundation | Average Cost Range (per Square Foot) |
Alaskan slab | $8 to $14 |
Basement | $20 to $37 |
Block | $9 to $15 |
Crawl space | $6 to $18 |
Frost-protected | $8 to $12 |
Monolithic slab | $4 to $14 |
Pier and beam | $5 to $16 |
Stem wall | $6 to $12 |
Alaskan Slab Foundation
An Alaskan slab foundation is a thicker, deeper variation of a standard slab-on-grade foundation. This type is ideal for cold climates where freezing ground increases the risk of a foundation cracking. An Alaskan slab is also the ideal choice where soil and water conditions don’t allow for a full basement and where a home has a walkout basement instead.
Unlike a typical slab foundation, an Alaskan slab has deeper trenches around the perimeter for the footings. While the middle part is generally thinner than the edges, the entire slab is much thicker than standard slabs. The thicker design is more substantial and influences pricing due to the extra installation time and additional materials. Typical Alaskan concrete slab prices range from $8 to $14 per square foot.
Basement Foundation
A basement foundation is a deep foundation that offers additional living or storage space beneath the structure it supports. The construction process involves building footings, erecting walls, and pouring a concrete slab to connect all the components.
Basement foundations are the most expensive type of foundation, as they require additional materials and labor hours. Homeowners can expect to pay between $20 and $37 per square foot, not including vapor barriers, insulation, or finish work.
Areas with high water tables are not suitable for basements, since they would flood frequently. For areas where basements are permitted, basement foundations offer homeowners additional living space and an increased home value despite the higher upfront costs.
Block Foundation
Homeowners can have block foundations installed for an average cost of $9 to $15 per square foot. This type of foundation offers several key benefits. To start, it can support more weight than a poured foundation, making it ideal for larger homes. It also offers extreme durability and a long lifespan when installed properly and routinely maintained. As a bonus, block foundations allow for more straightforward repairs than poured varieties.
However, if not correctly sealed, a block foundation can be more susceptible to moisture infiltration. Cinder blocks also don’t offer the same smooth finish as poured concrete, which can take away from the aesthetics of a home.
Crawl Space Foundation
A crawl space is a raised foundation that provides a gap between a home’s lowest floor and the ground. While the space isn’t typically tall enough to allow standing, it offers an area for utilities and storage in some scenarios.
The construction process uses fewer materials than other foundation types. The walls can be built using solid concrete, cinder, or concrete blocks. A crawl space foundation doesn’t typically have a full concrete slab. But if there is a slab, it’s much thinner than a standard pour.
Pricing ranges from $6 to $18 per square foot for a concrete crawl space foundation, depending on the size, depth, and soil conditions. Adding vents, insulation, or a sump pump will also impact the final price.
Frost-Protected Shallow Foundation
In some areas, additional insulation is needed, which is where a frost-protected shallow foundation comes in handy. These typically cost between $8 and $12 per square foot. With additional insulation, frost-protected foundations are ideal for frigid climates where foundations can experience structural damage due to excessive and deep ground freezing. They are similar to Alaskan-style slabs but more cost-effective.
During construction, at least 2 inches of rigid polystyrene insulation are installed beneath the foundation. While the footings may need to go deeper to sit below the frost line, the entire foundation can be poured all at once, saving labor hours.
Frost-protected shallow foundations suit various building types, including commercial and residential properties. However, there might be better choices for properties with moisture challenges, as drainage can be an issue.
Monolithic Slab Foundation
As its name suggests, a monolithic slab foundation is poured simultaneously. The central part of the slab is of standard thickness, while the edges are thicker to provide additional support. It’s one of the most affordable foundations, with monolithic slab foundation costs ranging from $4 to $6 per square foot.
Since it’s poured all at once, the construction process is usually faster than with other foundation types that need multiple pours. Monolithic slabs also require less maintenance, as they have fewer joints and seams, reducing the chance of leaks or cracks.
Monolithic slabs are best suited for areas where the ground doesn’t freeze. Stable soil is also essential. While this type of foundation is versatile and ideal for garages, sheds, and small homes, it does not support the construction of a basement.
Pier and Beam Foundation
A pier and beam foundation is an older type of foundation. It’s considered a crawl space foundation that uses wooden or steel beams supported by piers with a thin concrete slab poured on top. It creates a space beneath the structure that can be helpful for certain utilities and maintenance tasks.
However, a pier and beam foundation isn’t suitable for all soil types or in areas with frequent soil shifts, high water tables, or earthquakes. This foundation type doesn’t offer the same level of stability as others and is decreasing in popularity as a result. Homeowners can expect to pay between $5 and $16 per square foot for this type of foundation.
Stem Wall Foundation
As another type of crawl space, a stem wall foundation has vertical walls that raise a home above ground level. This design either creates a crawl space beneath the house or allows it to be situated in rugged areas where other foundation types won’t work.
Stem wall foundations are also known as frost walls or T-shaped foundations. They’re especially helpful in areas prone to extreme ground freezing while also being useful on uneven terrain or hillsides. Stem wall foundations are versatile and can be used with a variety of home architectural designs. A stem wall foundation ranges from $6 to $12 per square foot.
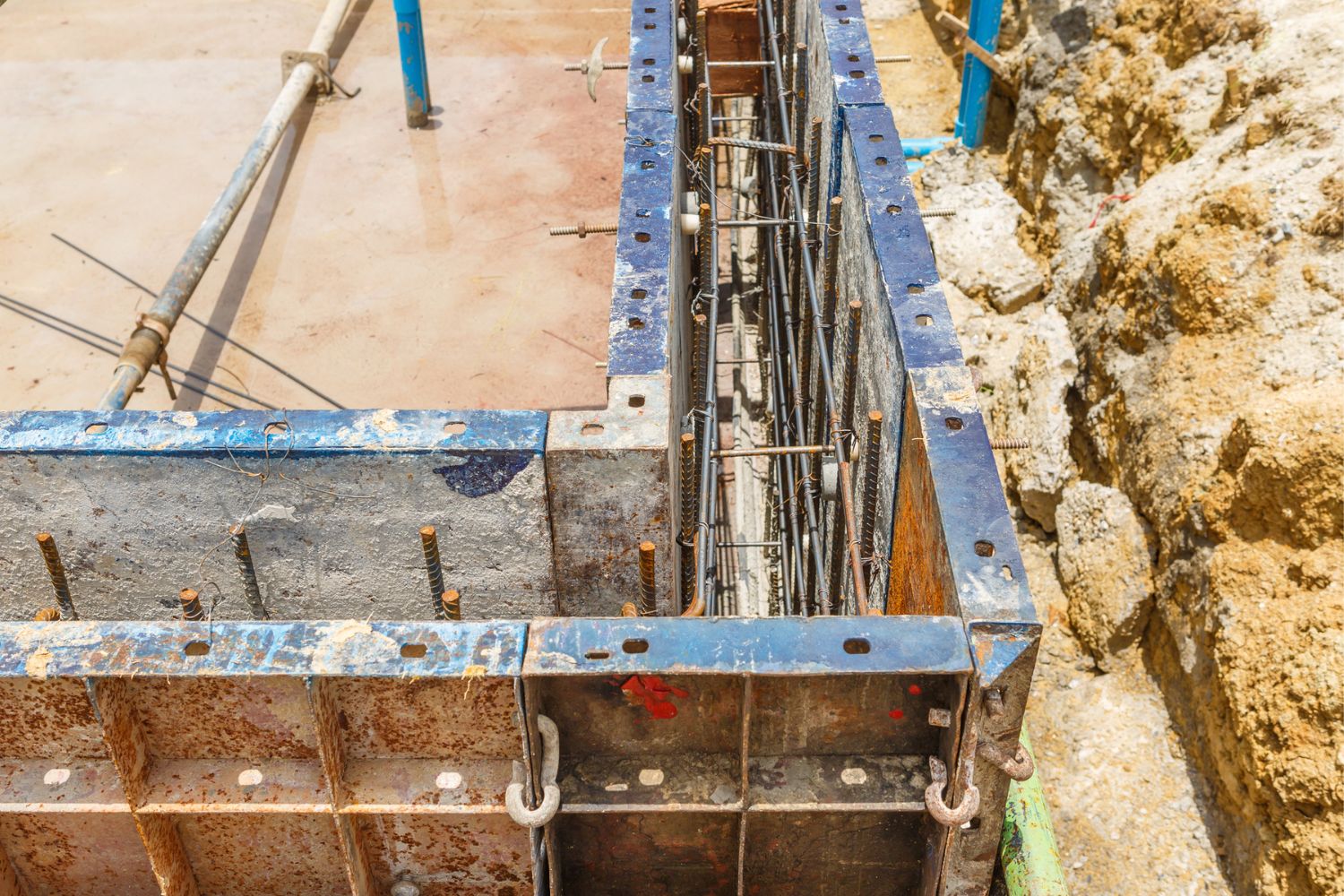
Benefits of Choosing to Build a Strong Foundation
The decision to build a solid and sturdy foundation comes with many benefits. Homeowners can enjoy protection from extreme weather, structural support to their house, added insulation and waterproofing, and even pest prevention.
Protection from Extreme Weather
Building a solid basement foundation is vital for a home’s protection from extreme weather and geological events like earthquakes. Rapid influxes of water from storms can destabilize the ground around and beneath a home, while strong winds and seismic activities can exert tremendous pressure on a house, potentially causing it to crumble.
A strong foundation makes it more likely that a house will remain anchored during a high-wind event or geological threat. In earthquake-prone areas, additional safety measures can be taken to strengthen the foundation even more, such as adding extra steel reinforcements, specific bolts and braces, and shock-absorbing components. Additionally, foundations that raise a home above ground level can avoid intrusion water during storm surges or flash floods.
While building a strong foundation comes with an added cost, it can mean the difference between life and death during extreme weather and earthquakes.
Structural Support and Longevity
A weak foundation puts a home at risk in several ways. Cracks in the walls and ceilings, uneven floors, and bowing walls are more likely to occur. A weak foundation can also allow water to enter a home, leading to serious problems such as mold, mildew, and wood rot. Over time, a house can diminish in value due to a weak foundation that requires expensive and premature repairs.
Building a strong foundation offers sound structural support and longevity. Homeowners can worry less about moisture issues and uneven settling. Additionally, homes with a strong foundation often have higher market values and extended lifespans while requiring less maintenance.
Insulation
Without proper insulation, homes lose significant heat during the winter and take in unwanted heat during the summer, leading to higher energy costs. A lack of insulation can also result in condensation buildup in the foundation. Excess moisture can lead to mold and mildew, which can cause respiratory issues for a home’s occupants.
By building a strong foundation using certain materials, such as insulated concrete forms or rigid foam, homeowners can feel confident that both the structural integrity and energy efficiency of their homes. Energy bills will be lowered, and HVAC systems will have a longer operational life with a reduced workload. Added insulation from a foundation will also protect.against moisture, creating a safer and more comfortable living environment.
Waterproofing
When it comes to any foundation, waterproofing is an exceptional benefit. But this feature is especially prevalent in a strong foundation. A strong foundation offers enhanced durability and can better resist moisture and hydrostatic pressure erosion and wear. A well-constructed foundation is also less prone to developing cracks, offering fewer entry points for water. Strong foundations typically incorporate better drainage solutions as well.
On the other hand, weaker foundations are more susceptible to water damage. They may experience severe cracks or even collapse due to water-induced damage. Such scenarios come with increased maintenance costs and the potential for reduced property values in addition to safety risks for residents. Ensuring that a home rests on a strong and durable foundation helps homeowners worry less about the safety of their home and its residents and avoid potentially expensive repair costs.
Pest Prevention
Many types of pests can enter a home through its foundation, especially one that is cracked or deteriorating. From transmitting diseases and causing allergic reactions to contaminating food, pests bring many health concerns.
Some pests can also cause structural damage to a home, including wood and electrical damage. They can leave behind unpleasant odors, and listening to the sounds of scurrying rodents can make a home’s residents feel uneasy.
However, a solid foundation without cracks or gaps offers fewer opportunities for pests like rodents, termites, and ants to work their way into a home. Strong foundations also tend to feature better waterproofing, which means less moisture that could attract pests.
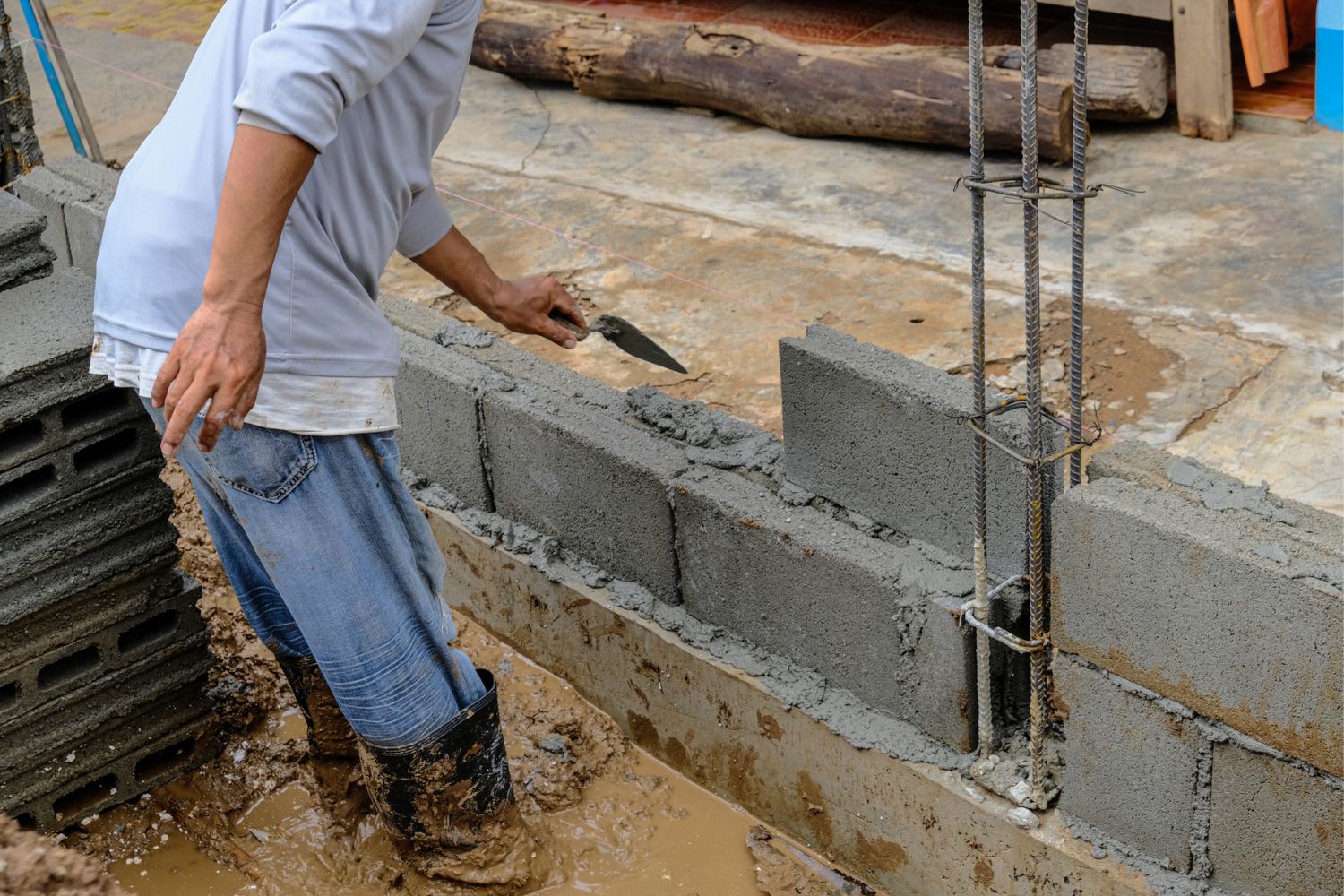
Foundation Construction: DIY vs. Hiring a Professional
When it comes to foundation construction, many homeowners might wonder if a do-it-yourself approach is an option for a small slab under a shed. While that can be an option for the most experienced DIYer who has all the time and resources to mix and pour concrete for a DIY foundation, most homeowners’ projects require professional know-how.
For major foundation projects like basements, it’s necessary for homeowners to hire a professional who is licensed and experienced at constructing a key part of a home. Even a slab-on-grade foundation is best left to the pros, who have all the necessary equipment to complete the project.
Even affordable concrete work is messy and more delicate than expected, so homeowners typically prefer to leave this project to those who can make short work of a long project. The process to start and finish a foundation is complex and requires knowledge of local building codes, soil types, drainage systems, and more.
Given the challenges, it’s evident that hiring foundation contractors is the better option.
They bring expertise, experience, and the right equipment to the job. Their knowledge ensures that the foundation is not just built but that it’s built to last, keeping the structure safe and stable for years to come.
How to Save Money on Foundation Cost
Building a foundation can be a significant investment, but homeowners can find ways to lay a strong foundation without overspending. These money-saving tips are helpful for homeowners to consider when researching foundation costs.
- Shop around. Contact different contractors for at least three separate foundation quotes. This approach will allow you to compare not only costs but overall value.
- Use local materials. Reduce transportation costs by shopping for local materials if there is anything you can purchase on your own.
- Understand cement pricing. Take some time to learn about current market prices for cement and other essential materials to help negotiate with suppliers and choose cement costing within your budget.
- Opt for simple designs. A simple foundation design can save on materials and labor costs, so it’s worth reviewing ways to maximize space with a more rectangular or square shape.
- Don’t skimp on prep. A well-prepared construction site can reduce unexpected costs. Make sure the contractor is on board to clear the area of debris and obstacles before the work begins. Or reduce costs by opting to prep the site yourself, if you have the time and equipment needed.
- Keep up on maintenance. Regularly inspecting and maintaining a foundation can prevent minor issues from becoming major problems that cost more down the road.
- Address cracks early. Should a routine inspection uncover a crack, addressing the issue immediately can save significant money in the long run. Foundation crack repair costs tend to rise as time goes on.
Though it’s not a money-saving tip, homeowners may want to apply for one of the best home equity loans through lenders like U.S. Bank or Flagstar Bank, to finance the cost of building a foundation. Interest rates tend to be more reasonable and are often locked in. Financing construction or renovation projects can help homeowners keep cash reserves for other uses.
Questions to Ask About Foundation Construction
Laying a strong foundation requires more than materials. It needs proper planning and the right team. That’s why it’s so important for homeowners to vet potential construction companies before hiring one. Homeowners can use these questions to help narrow down a list of residential foundation contractors.
- How many years of experience do you have in foundation construction?
- Are you licensed and insured for foundation work?
- Do you offer an itemized estimate and invoice?
- Can you provide a list of references you’ve completed foundation projects for in the past?
- What type of foundations are you most experienced with?
- Will you obtain the necessary permits and schedule the inspections?
- How long do you anticipate my foundation project will take?
- Do I need to insulate my foundation?
- Do you offer any warranties or guarantees?
- How will you address potential foundation crack issues in the future?
- How do you manage the disposal of construction waste?
- What safety measures do you take during the construction process?
FAQs
With foundation costs playing an essential role in construction budgets, it’s important for homeowners to understand the factors determining the final price. This FAQ section offers additional insight and advice on foundation requirements, features, and costs.
Q. What is the most cost-effective house foundation?
If a full basement is not needed, then the most cost-effective house foundation is a monolithic slab foundation. It’s a one-pour design for both the footing and slab. This straightforward construction method requires fewer materials, reducing overall costs. Installation costs range from $5 to $12 per square foot, depending on the size of the home. Larger homes can reach up to $16 per square foot.
Q. Can I pour my own foundation?
Pouring a foundation requires extensive knowledge of concrete mixtures, site prep, and proper leveling techniques. Most localities also require a permit for foundation work. Without the proper tools, experience, and knowledge, even a savvy DIYer may not be able to pour their own foundation without making a mistake that, come time for inspection, will need to be repaired or redone. Foundation work is best left to the pros.
Q. What is the most durable foundation for a house?
The most durable foundation for a house depends on several factors, including the property’s soil conditions, regional climate, and local building codes and regulations. However, a poured concrete foundation is typically considered the most durable. Other types of durable foundations include concrete block foundations, insulated concrete forms, and stone or masonry foundations.
Q. How long do poured concrete foundations last?
Several factors determine how long poured concrete foundations last, including the initial construction quality and local environmental conditions. While a poured concrete foundation can last at least 50 years—and up to 100 years or more—maintenance is critical. Homeowners should regularly inspect their foundation and promptly address any cracks, leaks, or other issues for optimal longevity.
Q. How do I hire the right foundation installer?
Hiring the right foundation installer starts with gathering multiple estimates. Homeowners are encouraged to ask for and check references to help ensure the installer’s experience matches their services. A great foundation installer will welcome questions and be open to discussing the project in depth. Finally, homeowners are advised to beware of vague clauses when reviewing estimates that could lead to hidden expenses.
Q. How deep does a concrete foundation need to be?
The ideal depth of a concrete foundation depends on climate conditions, the specific foundation type, and the construction site’s soil type. While some concrete foundations can be nearly surface level, others may need to be dug several feet deep. To ensure their foundation is dug to the appropriate depth, homeowners should verify local requirements to verify that the planned depth aligns with local building codes and standards.
Sources: Angi, HomeAdvisor, Fixr, Homeguide