

We may earn revenue from the products available on this page and participate in affiliate programs. Learn More ›
MIG vs. TIG welding is a debate that has been going on for decades. Both are types of arc welding commonly used by amateurs and professionals alike. Both offer versatility and relatively affordable equipment. So which is best?
Even though they sound similar—and the welding machines look alike at first glance—they are far from the same. In truth, the question of which type of welding is best depends upon which is the most appropriate for the job at hand.
Understanding the difference between MIG and TIG welding is key to the success of any project, and that’s what beginner welders in particular can learn from this article.
What is MIG welding?
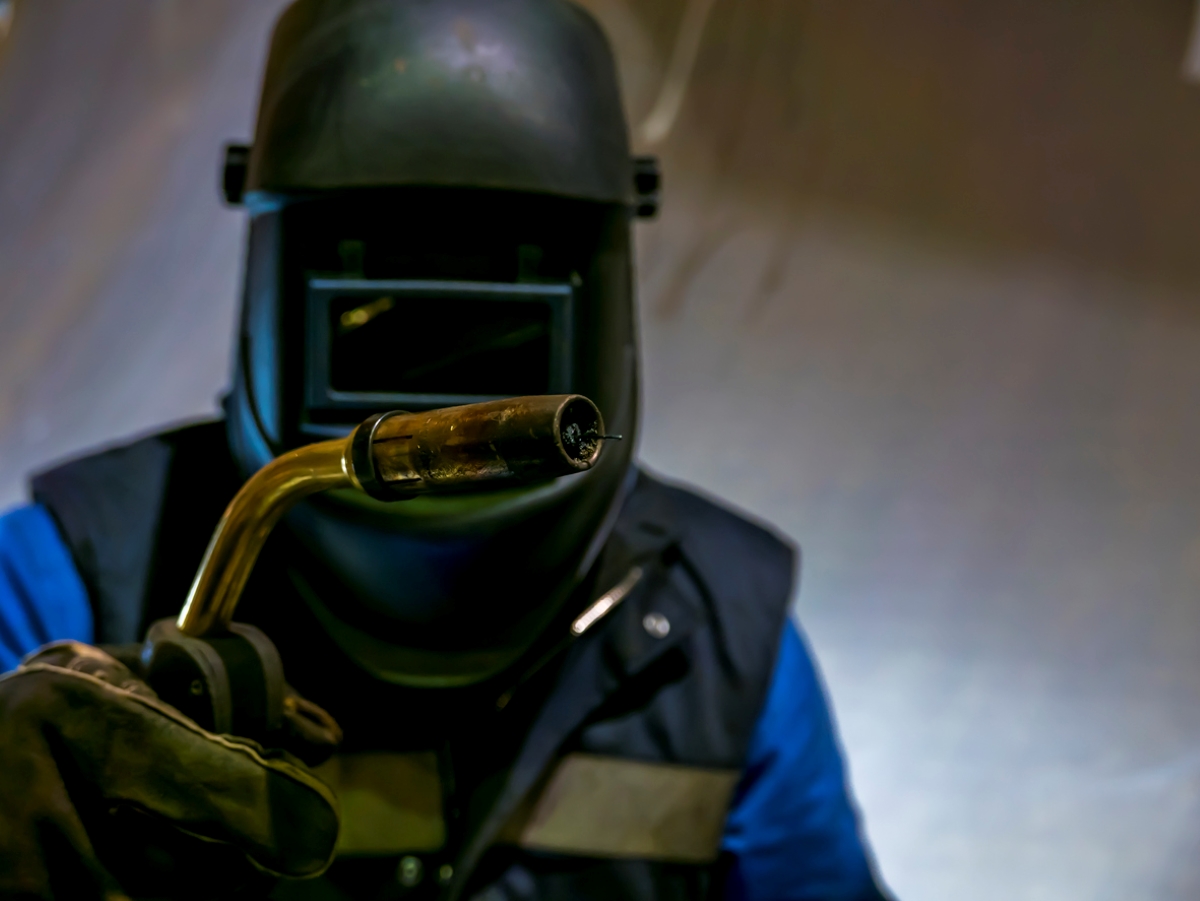
MIG stands for “metal inert gas,” and it’s also known as gas metal arc welding (GMAW). MIG welding machines generate a powerful electrical current that runs through a handheld torch. The torch supplies the welding gas and automatically feeds the MIG welding wire. This wire creates an electrical arc that melts the metal being joined and provides filler material to strengthen the joint. A ground clamp is attached to the workpiece to protect the welder from shocks.
Welding Gas
MIG welding gases are inert, so they have no impact on the chemical reaction within a weld. The most common is a mix of argon and carbon dioxide. The purpose of MIG welding gas (also called shield gas) is to protect the molten metal (the weld pool) from impurities present in the air. Hydrogen, nitrogen, and oxygen in the air around us can cause excessive spatter (molten metal thrown out of the weld) and porosity (air bubbles within a weld), the latter of which creates weaknesses in the finished job.
Not all MIG welders require a separate gas supply. With gasless MIG (or flux-core welding), the welding wire is coated with chemicals that form their own shield as the wire melts.
Weld Speed
Speed is an important factor when it comes to the question of TIG vs. MIG welding, and the latter is by far the faster of the two. A MIG welding machine feeds welding wire through the torch automatically, at a speed set by the user. Beginners can slow the wire to suit their skill level, while professionals can speed it up to maximize productivity.
One drawback of MIG welding is that it doesn’t produce such a neat weld, so extra time may be required to clean things up for painting or electroplating.
Weld Strength
Any properly formed weld is extremely strong. As an old adage says, the weld is actually stronger than the original metal. This is true of any good MIG weld, but care is required. Although MIG welding produces a comparatively large and easy-to-manage pool of molten metal, trying to weld too quickly can produce uneven penetration that leads to weaknesses.
Protection offered by the shield gas is a vital element. Any wind can disrupt this bubble and let in impurities, so standard MIG welding cannot be performed outdoors. One solution for this is a gasless MIG welder, although these can’t be used for MIG welding aluminum.
Our Recommendation: Forney Easy Weld 140 FC-i Flux-Core Wire Welder at Amazon for $250.24.
This popular, high-quality MIG welder is light, easy to use, and offers the performance necessary for a wide range of home and professional welding tasks.
What is TIG welding?
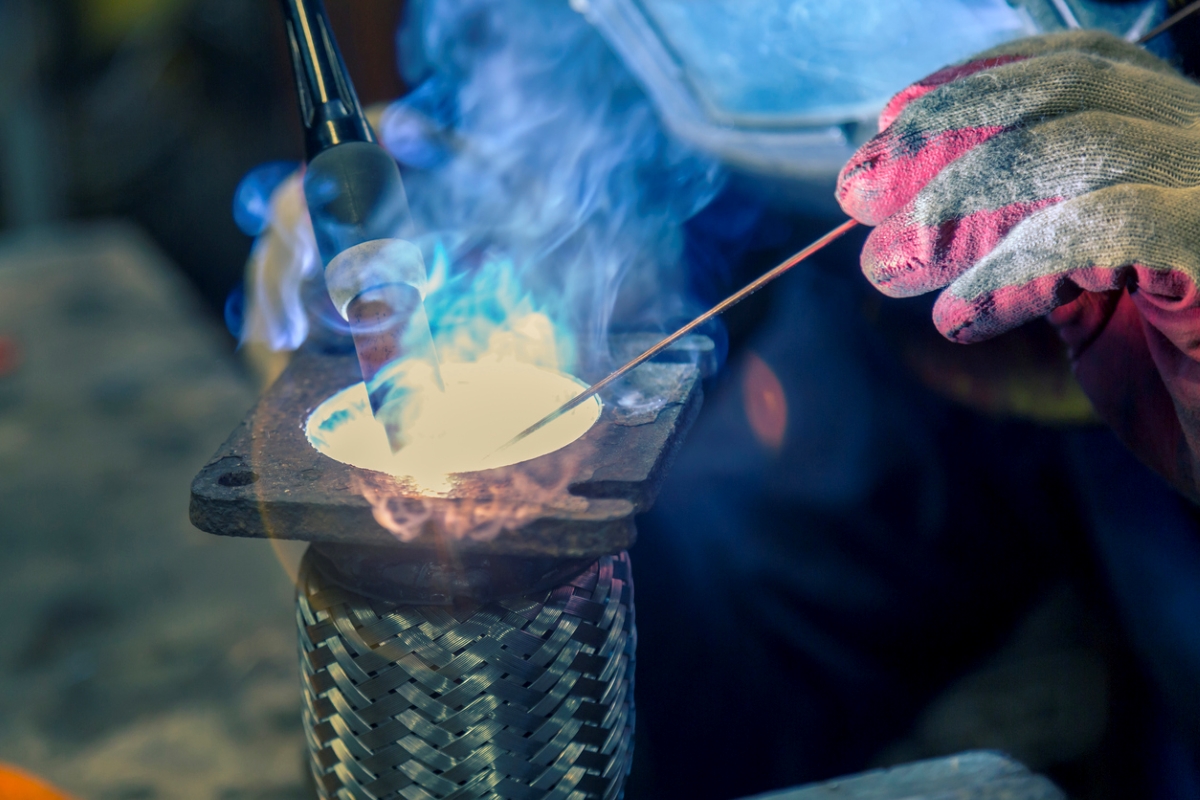
TIG stands for “tungsten inert gas,” and it’s also known as gas tungsten arc welding (GTAW). With TIG welding, the electrode delivering the electrical charge is made of tungsten, and (unlike MIG wire) it is non-consumable. An extra filler rod must be used as a result, which is held in the welder’s other hand. Coordinating the two demands greater concentration than when working with MIG.
Welding Gas
As with MIG welding, TIG welding requires gas to shield the weld from impurities. It also helps prevent the fixed TIG electrode from overheating. TIG welding gas is normally composed of argon or a mix of argon and helium (another inert gas). Argon and hydrogen are used when TIG welding stainless steel.
Argon and argon/helium shields are heavier than the argon/carbon dioxide mix commonly used with MIG welding, so it’s possible to TIG weld outdoors in calm conditions. However, it can still be a challenge. One widely available solution is a combo machine designed for outdoor use that includes stick welding, another option among the different types of welding.
Weld Speed
TIG welding is a slower process than MIG welding. This is partly due to welders’ need to coordinate the actions of both hands. There’s also the physical restriction of manually feeding the filler rods into the weld pool one at a time. For these reasons, it isn’t possible to TIG weld as quickly as with MIG’s automated wire.
The upside of TIG welding is greater control. The weld pool is comparatively small, making TIG a better choice when the appearance of a weld is important. This process also makes it possible to weld thinner material than can be done with MIG.
Weld Strength
Because TIG welding produces smaller and neater welds than MIG, it’s ideal for welding thinner materials. Also, the intensity of the welds penetrates material more deeply, so TIG weld strength is greater.
This is particularly true when TIG welding lightweight aluminum, as well as when working with smaller dimensions. MIG can simply be too powerful and can burn right through the material, whereas TIG provides the necessary precision.
Our Recommendation: AHP AlphaTIG 203XI at Amazon for $750.
This versatile machine can produce precision welds in steel, stainless steel, and aluminum, and has the added bonus of stick welding capability.
MIG welding is best for joining thick or large materials, while TIG welding is better for thin or small pieces.
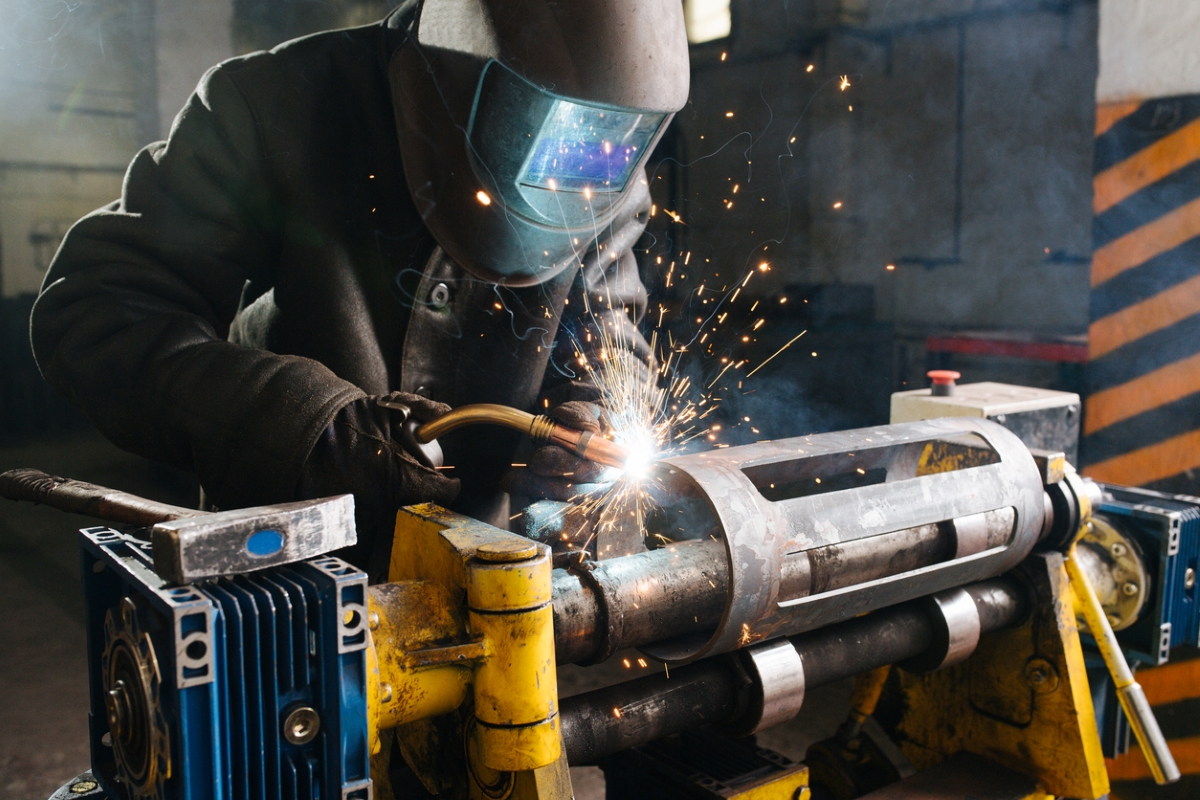
Both MIG and TIG can produce a variety of different types of welds in steel, stainless steel, and aluminum. Generally speaking, however, the speed and power of MIG welding is better suited to more substantial projects. MIG is a great choice for hobby welders interested in auto repair, building steel furniture, or creating steel sculptures for the garden.
While MIG welding stainless steel and aluminum is possible, TIG welding is generally considered the better option with these materials. Stainless steel and aluminum are more susceptible to heat variations and can be tricky to weld well. When thin stock is used, TIG offers a higher degree of control and results in smaller, neater welds. Once the technique is mastered, TIG welders can achieve a fine finish requiring little or no clean-up work before finishing.
RELATED: A DIY-Friendly Approach to Welding? We Tested the YesWelder MIG-205DS to See If It’s Worth It
Because TIG welding is more technically demanding, MIG is easier to learn for beginners.
MIG welding is invariably considered the best type of welding for beginners. The technique is easier to learn and more forgiving. Most welders start out working with ordinary steel (aka mild steel), which the MIG welding process is ideal for. High quality MIG welding equipment suitable for beginners is usually less expensive than TIG welding equipment.
TIG welding requires both hands, and while the power control may be located on the main unit, many machines use a foot pedal. This, of course, involves increased coordination. The reward for learning TIG welding is the ability to weld a wider range of materials and produce more precise, higher quality work. However, patience is required and the TIG process cannot be rushed. Taking a welding course is always a good idea for beginner welders and highly recommended for those who want to learn how to TIG weld.
MIG welds are generally weaker and less aesthetically pleasing than TIG welds.
The relative strengths and visual appeal of welds are often discussed in MIG vs. TIG welding discourse. The general consensus is that MIG welds are weaker and TIG welds are better-looking, but this can be somewhat misleading.
MIG welding is not weak; a well-formed MIG weld has tremendous strength and durability. It’s important to use the right process for any particular task, however. TIG welding can be stronger when joining small items and welding aluminum, but it’s seldom used for heavy-duty structures. MIG welding is more appropriate and provides all of the needed strength for such jobs.
While it is true that TIG welds are usually more aesthetically pleasing, it should be kept in mind that items being TIG welded are often lightweight, so these welds are naturally smaller. MIG welds are frequently larger and more raised, but there’s no inherent reason they can’t be smooth and neat.
MIG welding costs less than TIG overall.
A number of elements have an impact on the overall cost of MIG vs. TIG welding, but MIG usually works out cheaper from both a DIY and commercial point of view.
While low cost TIG welding machines are available and provide an affordable introduction to the process, high quality machines for those who intend to TIG weld regularly are generally around twice the price of an equivalent MIG welder. MIG welding wire is a little cheaper than TIG welding rods, though it isn’t usually a significant factor.
In commercial environments, speed of working can be a major factor. Not only is TIG slower, but parts to be welded need more careful preparation. As a result, job costs rise. It may also be the case that a skilled TIG welder receives higher pay than a MIG-only welder.
RELATED: The Best Welders for Beginners
When To Use MIG vs. TIG Welding
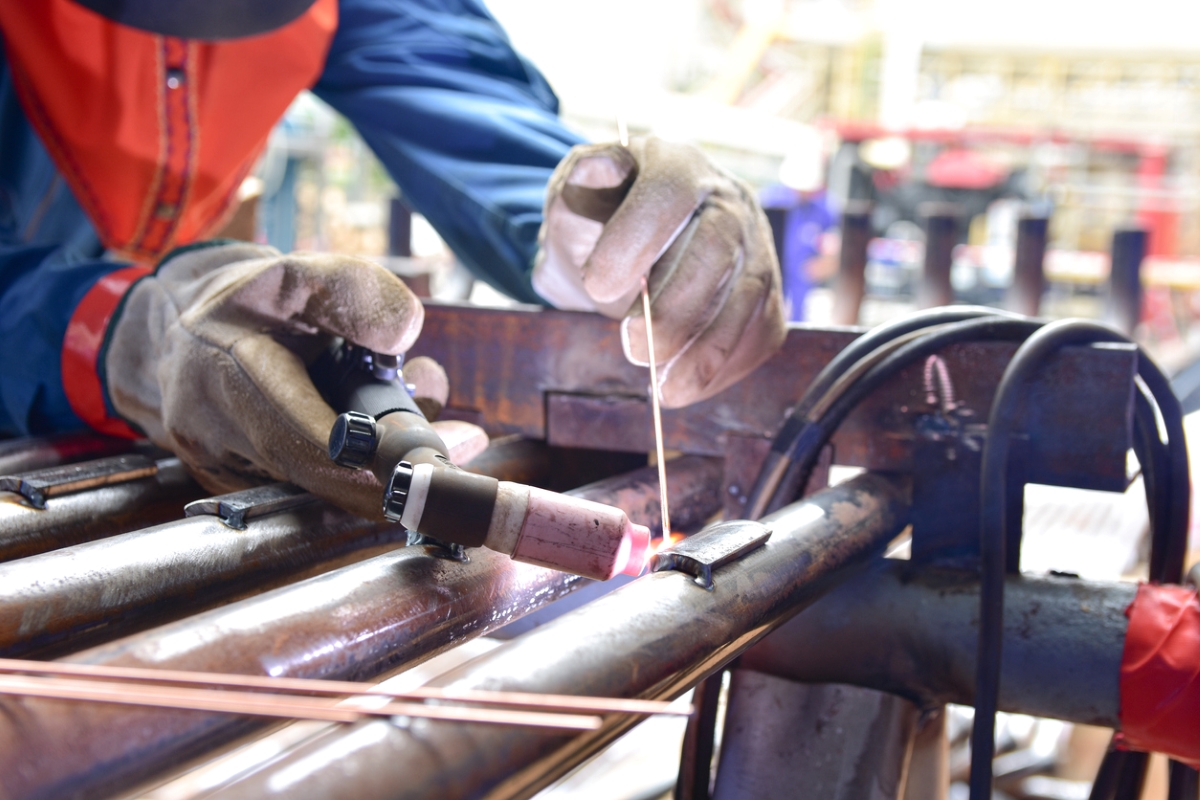
There isn’t really an overall winner in the MIG vs. TIG argument. Although these types of welding are interchangeable to some extent, each has its strengths and weaknesses. Understanding these pros and cons is the key to knowing which welding process will produce the best results. Although there are occasional exceptions, the following is a useful overview:
- Heavy-duty jobs: Both standard MIG and gasless (flux-core) welding are the best choice for larger jobs. They can deposit great quantities of filler quickly and weld substantial thicknesses in a single pass. While TIG welding can achieve the same in multiple passes, it’s rarely a practical solution, and applying weld on weld using TIG is much slower.
- Precision jobs: Mild steel, stainless steel, and aluminum can all be successfully MIG welded, but control can be difficult—particularly with thin sheet metal. It’s not unusual for beginners to burn holes through a workpiece. TIG welding offers greater precision, both in terms of the welding machine-provided adjustment and greater welder control.
- Long-run vs. small jobs: Each TIG welding rod is around 3 feet long, so this process can involve a lot of stopping and starting. By contrast, a MIG welding spool contains several hundred feet of wire. Given that MIG wire is fed automatically through the welding gun, MIG welding is almost always the better option for a long run of welding. TIG welding is excellent for small, detailed pieces, but it can be very time-consuming on larger jobs.
- One- two-handed operation: MIG welding is done with just one hand. TIG welding requires two. This may not be important in a workshop, although one-handed operation can be useful for steadying a workpiece, ability, or comfort. With awkward welding positions (more common jobsite welding), having another hand for balance might make the difference between safe and unsafe work. An out-of-control welding torch can be a very dangerous hazard.
At this point, it is worth mentioning welding safety and personal protective equipment (PPE). A welding helmet, welding jacket or apron, and proper welding gloves are all vital for avoiding burns and a painful type of eye injury known as “welder’s flash” or “arc eye.” Fortunately, the same high-quality welding PPE can be used for all forms of welding.
Final Thoughts
While both are excellent ways of joining metal, the MIG vs. TIG welding debate will likely continue. They both have their pros and cons, meaning neither one is “better” than the other overall.
From a beginner’s point of view, MIG welding is undoubtedly easier to learn than TIG. It’s more affordable, can accomplish most DIY welding tasks, and delivers strong, durable welds with a little practice.
A skilled welding professional will always produce a neater weld with TIG welding than they can with MIG, but that level of precision often isn’t necessary in your garage or yard. Most people who learn TIG welding will have started with MIG, anyway, moving on to TIG when a job demands it.
RELATED: The Best Work Boots for Men and Women, Tested
The prices listed here are accurate as of publication on 12/20/22.