We may earn revenue from the products available on this page and participate in affiliate programs. Learn More ›
Highlights
- The typical cost range to install a metal roof is $5,659 to $17,314, with a national average cost of $11,452.
- The exact cost will depend on the type of metal, the roof size and style, the cost of labor and permits, and the home’s geographic location.
- The benefits of installing a metal roof include lower homeowners insurance premiums, longevity, energy efficiency, resistance to weather and fire, and return on investment.
- Metal roof installation is not a project for a casual DIYer; not only can metal roof installation be dangerous for inexperienced homeowners, but DIY installation can void the roof’s warranty.
Time for a new roof? You’ll find lots of options on the market. If you’re tired of the default asphalt shingle roof but not interested in the high maintenance of wood shakes or the structural work needed for heavy tile or slate, consider the option of a metal roof. Once relegated to industrial and agricultural applications, metal roofs are popping up in residential areas with increasing frequency. That’s because metal roofs offer a bevy of benefits: They’re environmentally friendly, energy-efficient, come in a wide range of styles, and last between 70 and 100 years. The fact that the initial outlay for metal roofing is a bit higher than some roof types is justified by the fact that you’ll probably never need to replace it. These roofs can be designed and installed to create almost any look a homeowner wants.
Metal Roof Cost: How to Calculate the Cost of a Metal Roof
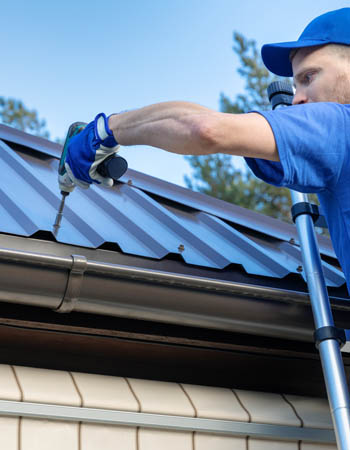
You may know the size of your home, and you may even know the square footage of your roof—but calculating the cost of a metal roof is a little more complicated. Roofing prices change with the demand for materials and the cost of acquiring them, and labor costs vary regionally and seasonally. As a base calculator, use the following formula:
Materials + Labor and Installation in My Area + Overhead = Total Cost of Metal Roofing Near Me
Each of these three components should make up one-third of your project cost.
As you begin calculating, keep in mind that roofers use a unique unit of measure called a roofing square to calculate material prices, equivalent to 100 square feet (a 10-foot by 10-foot square). This calculation will itemize the total material cost for that section, so the number of squares needed to cover your roof will drive the rest of the expenses. To accurately estimate, plan on over-ordering material by 5 to 20 percent to account for waste on cuts and any pattern matching. Labor costs will vary, so plan to collect multiple estimates with itemized cost lists before you choose. Overhead will include costs such as shipping, tools, permits, and insurance.
Factors in Calculating Metal Roof Cost
How much does a new roof cost? To accurately plan and budget for a metal roof, you’ll need to consider many of the same elements as you would with any other roofing style. Some of these costs are nonnegotiable, while others can be increased or reduced based on selections and some thorough price comparisons.
Geographic Location
Material and installation costs vary significantly based on where you live. New England, the West Coast, Hawaii, and Alaska are where roofing installation is most expensive. Prices tend to be lower in the Midwest and southern rural areas. Since your home location isn’t something you can change, your best plan is to seek out numerous estimates to make sure you’re getting the most competitive contract if you live in one of the more expensive regions.
Material Type and Form
Not all metal roofs are the same: There is actually a relatively wide range of metal materials that can be fashioned into roofing sheets or tiles, and what you choose can significantly influence the cost. The least expensive is an alloy called Galvalume, which can cost as little as $75 to $200 per roofing square. Galvanized steel will increase the cost to $150 to $350 per square, and aluminum can range from $150 to $600 per square. Steel, stone-coated steel, zinc, and tin all gradually increase in price, and the luxury materials like stainless steel ($400 to $1,200 per square) and copper ($800 to $1,500 per square) round out the higher end of the material costs. Lead tops the list at more than $1,000 per square, depending on the core material in the lead. Those materials do boast a longer lifespan and less maintenance, though.
Roofing Style
Metal roofs are available in several different configurations. The most basic style is sheet metal, which can be flat, ribbed, or crimped to change the appearance and function. Sheet metal, on average, costs $75 to $600 per roofing square, depending on the material. Standing seam metal roofs are strips or panels of metal whose edges have been folded together to create a ribbed seam. The additional craftsmanship of this style raises the cost to $200 to $1,000 per roofing square and results in a higher installation cost. Finally, metal roofing is available as strips that are pressed or stamped to look like individual shingles, shakes, or tiles, costing between $200 and $600 per roofing square.
Roof Size, Slope, and Pitch
The size of the roof will determine how much material you need to order and how much time it will take to install. Large roofs with complex designs and many sides will require a larger crew or more time, increasing labor costs.
The pitch of the slopes on the roof affects the amount of material you need to order, the method of installation, and the amount of safety equipment installers will need to use. Roofs with a steep pitch (greater than a 3-inch rise per foot) will cost more in labor, as it is more dangerous to work on, takes longer, and requires additional material. Roofs with a lower pitch (less than a 3-inch rise per foot) are the easiest to work on, as they are usually walkable and need less safety equipment and material. The most expensive roof pitch is a curved one: These roofs require additional safety equipment because it’s easier to lose one’s footing on a curved surface, and applying panels or shingles to a curved roof without damaging the materials is tricky and requires extra time and skill.
Underlayment
If your installer were to mount a metal roof directly onto the studs and sheathing of your home, you’d never sleep during a rainstorm again (and you’d also have leaks everywhere). Specially designed underlayment creates a barrier between the house and the roof, muffling sound, providing insulation, and stopping leaks. If your roof has exposed fasteners, specialized peel-and-stick gummy underlayment should be used to prevent leaks from fasteners subject to the weather. Underlayment will cost between $4 and $5 per square foot. Check with your contractor—this cost may be incorporated into the material or installation of the metal roof cost within the contract.
Labor and Installation
The labor cost for metal roof installation is significant—it can be as much as three to seven times the cost of the materials. The average labor cost is $3,000, but adding in pitched angles, complex structures, and size, this cost can range up to $10,000 or more. This should include the finish pieces of the roof like drip edges, ridge caps, flashing, fasteners, gable edges, ridge caps, and coatings.
Permits
Nearly every local government will require a building permit for a new roof. Because the roof is such a critical component of a house’s structure, the building department will want to ensure the building’s quality and materials (and assess the property taxes on your home if the roof constitutes an improvement). Consult your town’s building department for permit rates. If you live in a dues-paying homeowners association, there may be additional permits or approval to request if you’re changing the material or color of your roof; check these at the same time, so you don’t incur a fine later.
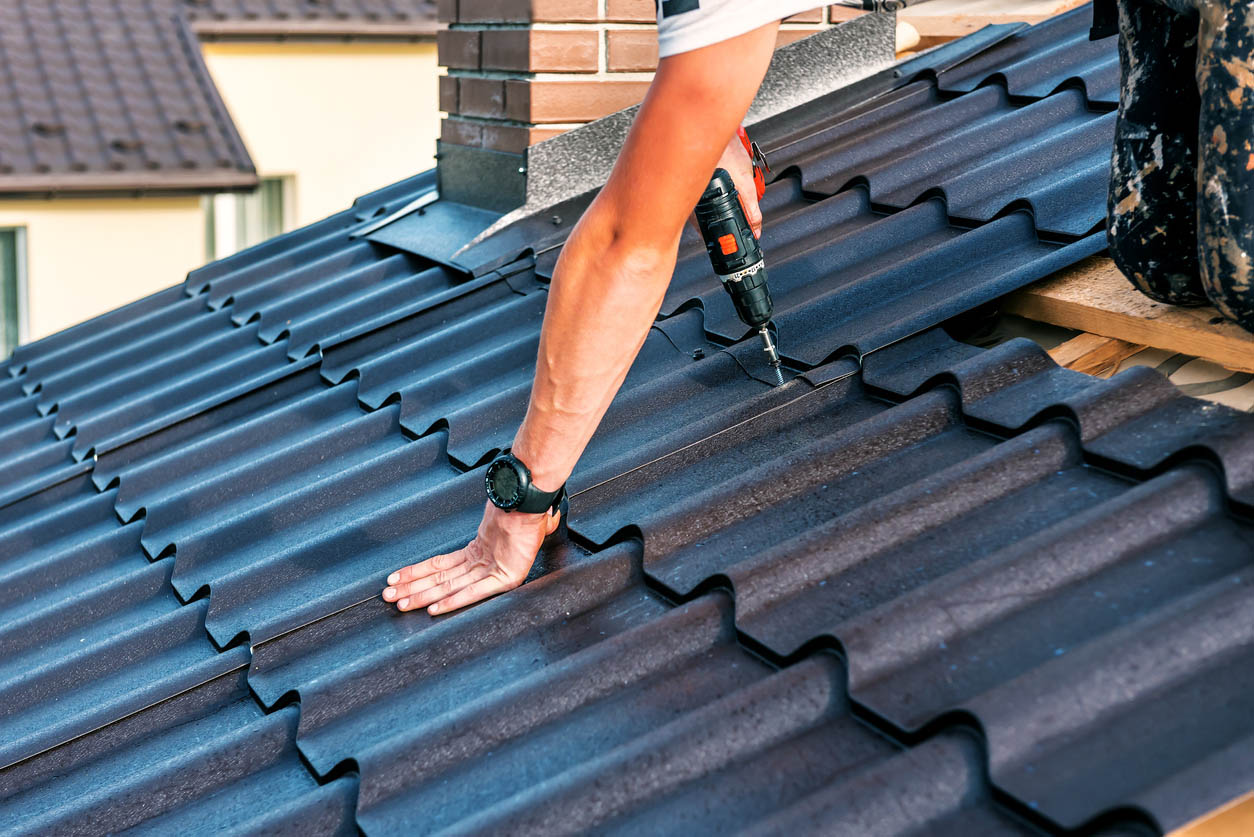
Additional Costs and Considerations
The materials, installation, and permits for a new metal roof aren’t the only costs to consider. Quality preparation and finish work can make the difference between a roof that just covers the house and one that complements the home and wows neighbors. While some of these elements are optional, they’re all essential to consider.
Painting or Coatings
Metal roofing arrives with a coating of zinc or a combination of aluminum and zinc. This will protect your roof for a while. Still, it’s an option to add an additional polymer coating layer for extra protection and longevity and to prevent hazing, which can occur as the metal oxidizes. Alternatively, some homeowners have a particular image of a metal roof in their mind that can’t be met with bare metal, and those homeowners have the option to paint their roof. The average cost to seal or paint a roof ranges between $300 to $1,500 based on the size of the roof and the grade of the coating selected.
Cost to Remove an Existing Roof
If you’re replacing an existing roof, you’ll need to include the cost of removing the old one and carting away the debris. Removal will add $1,000 to $1,500 to the total project budget. Depending on the type of roof being removed, there may be some additional permits required to dispose of the material—a contractor should have this information, but it’s a good idea to check with the town to be sure.
Accessories
Most new roof installations will include gutters and hardware, but if you have skylights or solar panels, you’ll need to factor in the cost of replacing them or removing and reinstalling them. Your contractor may choose different configurations of panels to accommodate solar arrays or skylights, and other custom accessories will require careful planning, placement, materials, and labor.
Flashings, Vents, and Chimneys
One of the most important functions that a roof performs is to keep water and extreme temperatures out of a home—but it also allows an HVAC system and plumbing to work. The plumbing vent stack, vents for air conditioning units and laundry appliances, and chimneys from boilers may all egress through the roof. Working around these features will require expert installation methods. If a house is older, replacing the chimneys and vents themselves may be an added cost. The flashing around all of these items, as well as around windows, skylights, dormer windows, and roof valleys, add material and labor costs.
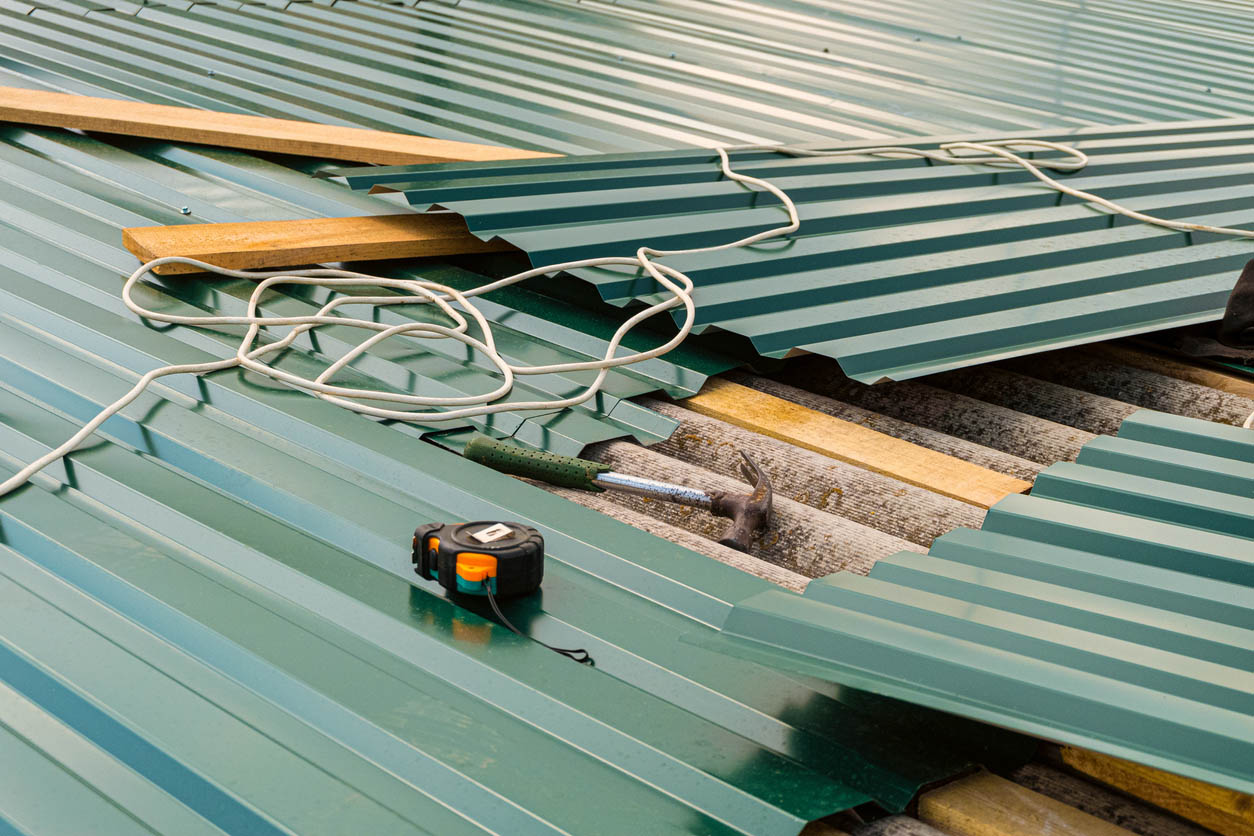
Metal Roof Cost: Types of Materials
The range of materials available for metal roofing is wider than you might think. Each material type and style has a unique look, along with individual benefits and drawbacks. You’ll want to consider the look you’re going for, the style of your home, and in some cases, how long you plan to remain in your home. While metal roofs are not significantly more expensive than other types, in the long run, the initial cost is a bit higher. If you’re planning to move soon, a luxury material for a metal roof may not be the best option.
Steel
A basic steel roof can cost as little as $75 to $350 per roofing square. Usually galvanized or coated in Galvalume, steel roofs are efficient, inexpensive, and available in both panels or shingles.
On the other hand, stainless steel is one of the more expensive options—$400 to $1,200 per roofing square—but with good reason. Stainless steel roofing, which comes in both sheets and tiles, resists rust and corrosion and is durable. It is used as the roofing and facing on large office buildings and skyscrapers (including the Chrysler Building in New York City) because it holds up well to weather and remains glossy and attractive.
Galvanized
A zinc-coated steel core results in a low-maintenance, durable roofing material that increases a home’s energy efficiency. Ringing up at $150 to $350 per roofing square, galvanized material resists impact denting (so it’s ideal for areas with frequent hail) and develops a patina over time. It can suffer from corrosion and may require some additional maintenance and recoating.
Galvalume
Galvalume also features a steel core but is covered with a material that is a combination of zinc and aluminum. It’s less expensive than galvanized material at $75 to $200 per square but is more corrosion resistant than plain steel. Galvalume is available in many colors (although without regular resealing, colors can fade) and is quite flexible compared to other materials, so it can be helpful in applications where curves or shaping are necessary.
Tin
Tin used to be a common roofing material, especially in situations where waterproofing was important. Today, most tin products are actually a steel core with a tin and zinc or tin and lead coating called Terne. Extremely durable and resistant to corrosion, Terne develops a gray patina with time and costs around $350 to $1,500 per square.
Aluminum
The cost of an aluminum roof varies heavily depending on whether you select sheets or shingles, running as little as $150 per square for sheets or as much as $600 per square for shingles. Naturally reflective, flexible, and recyclable, aluminum is one of the most naturally energy-efficient materials you can choose for your roof. You may see references to aluminum roof panels when you’re shopping; these products are designed to cover patios or porches and are sheets of aluminum with a foam core. Available in a range of colors and styles, these panels are insulated and come in DIY kits for $3,000 to $5,000.
Copper
Copper has a rich natural beauty, and combined with its long, low-maintenance lifespan and rust-free properties, this material is one of the most expensive roofing materials you can choose. In addition, copper is easily warped or dented during installation (though quite solid after it’s properly in place), so it requires a skilled professional and extra time to install. At $800 to $1,500 per square, it’s a classic, lovely option for many homes and an investment that will last.
Zinc
Zinc is used as a coating for other metal roof materials but can also stand alone as a covering. Zinc forms its own coating as it ages and oxidizes and has the unique quality of healing itself and reseal dents and scratches when they occur. It’s durable and long lasting. Zinc shingles fall at the lower end of the cost range ($600 per square), while standing seam installations can reach or surpass the higher end ($1,000 per square).
Lead
Although you don’t want it in your paint or water, lead makes an outstanding roofing material. While manufacturers have performed studies that show lead is a safe roofing material, it’s a good plan to check with the EPA or your local building department before purchasing to ensure there’s no problem installing it in your area. Most lead roofing features a copper or other metal core and a lead coating to cut down on the weight without losing the insulation value of the material. Lead installs well on flat and highly pitched roofs, resists corrosion, and develops a deep and beautiful patina. It’s available in shingles or panels and has the benefit of being easy to bend or form against unusual shapes, so it’s ideal for curved roofs or tight fits. At $1,000 or more per square, it’s a luxury choice, but one that will stand the test of time.
Rusted Metal
A rusty metal roof probably doesn’t sound appealing at first, but this material isn’t disintegrating or full of holes—it’s made from a type of steel called Corten that is pre-weathered to have a uniform rusted color. The rust layer actually protects the steel core while looking charmingly rustic. It’s available in panels of various textures. This choice is not ideal for coastal areas; while the roof will repel water, snow, hail, and other weather, the blowing saltwater near the ocean will cause the rusted metal to deteriorate quickly.
Sheet Metal
Most of the material types are available in sheet form. Sheet metal comes in different gauges, or thicknesses, for various applications. The lower the gauge, the thicker the metal is. Most sheet metal for commercial and residential roofing averages between 24- and 30-gauge. These roofs are installed with exposed fasteners, creating a rustic look. They can be painted or left unpainted. The metal can be pressed into different styles, and ribbed, corrugated, and crimped are common styles. Sheet metal is the least expensive type of roofing because it is generally easy to cut and shape and runs between $75 and $600 per roofing square.
Aluminum or Metal Shingles and Shakes
Metal roofs can be constructed by pressing shingles, shakes, or tiles for a more traditional roof appearance with less maintenance than wood, stone, or asphalt shingles. These can’t be used on flat or low-pitched roofs. The shingle-style strips are called modular press-formed granular or stone-coated and are made from 26-gauge steel and stamped with a texture that looks like a traditional asphalt shingle. Other press forms include metal Spanish tile, which is lighter and less costly than real Spanish tiles, and a metal slate, which has the appearance of real slate but is far lighter, easier to maintain, and less expensive. These options provide a more traditional roof while maintaining the efficiency, cost, and durability of a metal roof. In addition, they can help sidestep some homeowners associations that prohibit vertically striped traditional metal roofs. Slightly more expensive to install than sheet metal roofing, a shingle or shake roof can last as long as 40 years with minimal maintenance and is far more resistant to corrosion and leaks than panels. Depending on the style, metal shingles and shakes cost between $200 and $600 per roofing square.
Standing Seam
This style allows for expansion and contraction of the metal in heat and cold without cracking or stressing the metal. Constructed from galvanized or Galvalume steel, aluminum, copper, or zinc, standing seam roofs have a modern farmhouse look. They are available in 18- to 28-gauge metal for commercial applications and 24- to 26-gauge pieces for residential. They can be attached with invisible clip fasteners or exposed fasteners. These panels are constructed by folding the edges of two panels together to hook together, creating a mobile yet watertight seam. Some snap together, while others simply fold, creating an attractive vertical pattern on the roof. These average between $200 and $1,000 per roofing square.
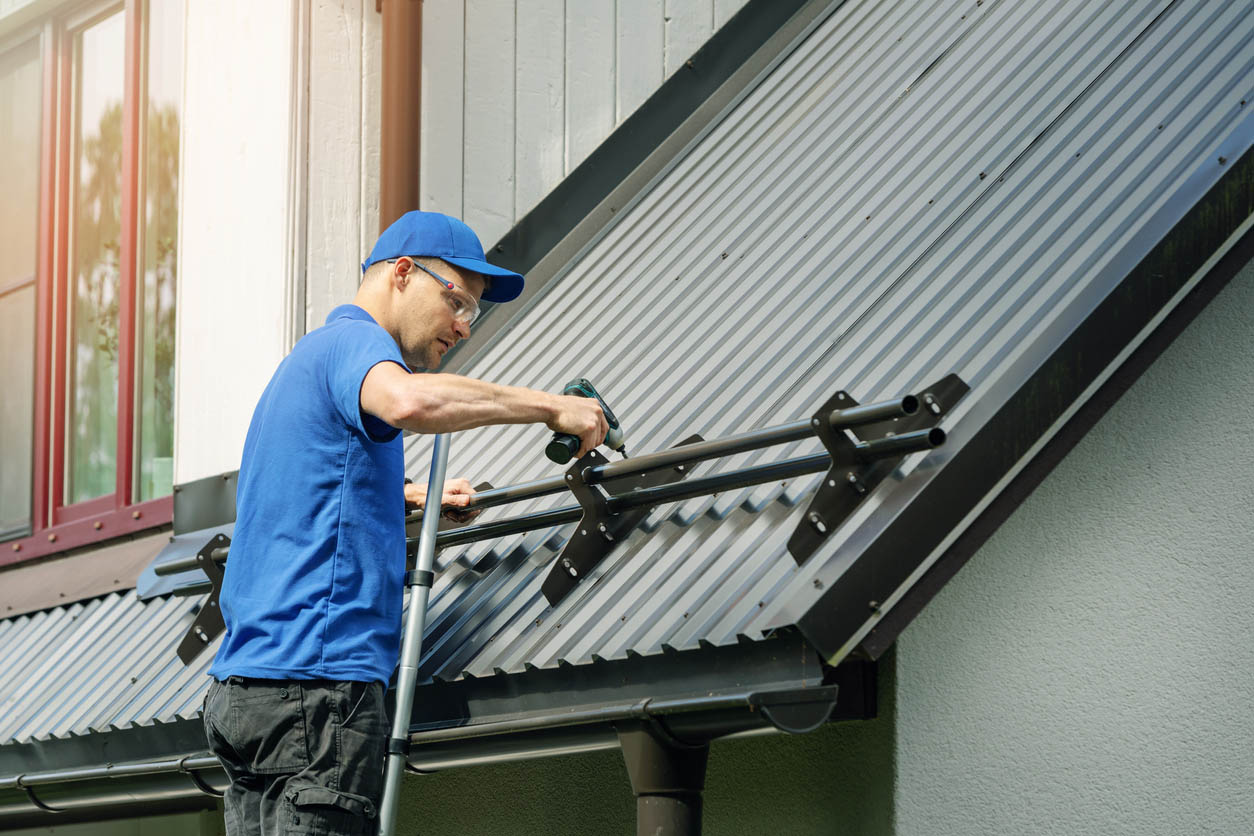
Metal Roof Cost: Benefits of a Metal Roof
Metal roofing is attractive and has some obvious benefits, especially in snowy climates where the snow slides right off. But metal roofs are more expensive at the outset than other roofing options. In truth, metal roofing offers much more beyond its attractive look; this roof style provides environmental, financial, and safety benefits.
Return on Investment
Homebuyers often eye the roofs of prospective homes critically. The buyers are about to invest most of their savings and commit to years of mortgage debt, and they do not want to be surprised by a roof failure a few years in. Realtors suggest that homeowners can recoup as much as 95 percent of the cost of a metal roof during resale. If buyers know they won’t have to replace the roof in a few years (or possibly ever), they’re more likely to be willing to pay a premium for that security.
Tax Credits
Many states and some federal programs offer tax rebates or credits that encourage the installation of environmentally friendly or energy-efficient products in the home. Because of the high recyclability of metal roofing, low carbon footprint of production, and energy efficiency of homes with metal roofs, you may qualify for a tax reduction for choosing this option.
Less Costly Homeowners Insurance
Homeowners insurance companies will often grant as much as a 30 percent discount on homes featuring metal roofs, counting on their weather- and fire-resistant properties along with their lengthy lifespans to reduce the likelihood of a damage claim.
Long-Lasting, Cost-Effective Roofing Option
Metal roofs last a long time—longer than any other roofing material—and look good as they age. When correctly installed and maintained, metal roofs have an expected lifespan of 40 to 60 or more years and frequently carry warranties of 30 to 50 years from the manufacturer. Wood, asphalt, and concrete roof materials require far more maintenance and require more frequent replacement; in a side-by-side comparison of initial cost plus yearly maintenance, the total cost of a concrete roof over a 40-year lifespan is between $18,000 and $28,000, while the cost of a metal roof over the same period is between $15,000 and $18,000—even though the average initial cost of the concrete roof was $4,000 less than the metal roof. Over time, the metal roof is less expensive per year than its counterparts.
Energy Efficiency
Some of the higher upfront costs of metal roofs can be immediately offset with lower heating and cooling costs. Metal reflects solar heat instead of absorbing it as asphalt and wood do. In addition, the panels keep heat from escaping from the attic in the winter. Together these qualities can reduce cooling costs by as much as 40 percent.
Wind, Lightning, and Fire Resistance
If installed correctly, many metal roofs can withstand wind up to 140 miles per hour. Especially in areas prone to hurricanes and other severe weather, this is an enormous benefit and something other roofing material can’t even come close to. In addition, metal roofing will not spark or catch fire as a result of a lightning strike or wildfire, and it resists not only fire but also smoke damage, protecting the integrity of the structure in case of fire elsewhere.
Environmentally Friendly
Most metal roofing comprises at least 25 percent recycled materials (sometimes as much as 70 percent) and is 100 percent recyclable. Steel roofing can be recycled again and again without losing any strength. This type of roofing is a more sustainable alternative to traditional asphalt shingles, which need to be replaced every 15 to 20 years and can’t be recycled. Because they are petroleum products, these shingles will never biodegrade, and they use valuable resources in their production. Metal roofing reduces fossil fuel dependency and keeps garbage out of the landfill.
Ideal for Low-Pitched Roofs
Flat or low-pitched roofs suffer from rain pooling and snow piles, leading to leaks, ice dams, and roof failure. Well-maintained metal roofs are impervious to water puddles, and they permit snow to slide off on its own or easily with a roof rake. While the metal roof must be installed correctly with the proper underlayment to be effective, it’s a great solution for rooflines that don’t have enough slope to drain easily on their own.

Metal Roof Cost: DIY vs. Hiring a Professional
The sheets of corrugated metal at the home improvement store may look manageable, hanging there by the boxes of fasteners that look just like other hardware you’ve used. Maybe you’ve helped a neighbor install asphalt shingles, and you’re comfortable with heights. It seems so easy! But when was the last time you climbed an extension ladder while holding on to what is essentially a giant, sharp-edged metal sail? Whether you’ve chosen sheet metal, pressed shingles, or standing seam, metal roofing requires some specialized handling to place, trim, fasten, and finish with the watertight, polished finish you’re looking for (along with great balance on that ladder). In addition, many metal roofing companies require professional installation for the warranty to be valid—and when you’re talking about a 50-year warranty, that’s a significant matter. This is not to say that you can’t assist your contractor or do it yourself if you have the knowledge, tools, and experience. But for safety, peace of mind, and the sake of the warranty, you’re better off hiring a professional who really knows how to install metal roofing.
Metal Roof Cost: How to Save Money on a Metal Roof
Replacing a roof is never inexpensive, and installing a metal roof is, at the outset, one of the most expensive options. This doesn’t mean there aren’t ways to save, however. Some savvy questions and choices can make writing the check a little less painful.
- Choose your timing: Don’t wait until your existing roof is falling apart to start researching. That way, you can take advantage of the “slow season” to reduce material and labor costs.
- If your existing roof is asphalt shingle, ask your contractor if it is in good enough condition to apply the metal roofing on top to save removal and disposal costs.
- Choose less-expensive materials, and ask about accessories or finishes that are more economical.
- Seek out numerous estimates and choose one with the right balance of excellent reputation and craft with cost.
- Are you replacing a roof that was damaged? Check into filing an insurance claim. Your homeowners insurance may cover some of the replacement costs.
- Ask for a better price. Labor is a significant portion of the cost of a metal roof. While you don’t want to be disrespectful to the professionals you’ve chosen to install yours, the cost of the labor may be negotiable if you’re willing to bend on timelines.
- Check with manufacturers of metal roofs that you admire. They may have recommendations for contractors they’ve supplied before, which will help you know that your contractor is experienced and allow you to negotiate more confidently.
Questions to Ask About the Cost of a Metal Roof
Installing a metal roof is, in many cases, an art form. Before choosing your artist, you’ll want to have answers to questions about cost, safety, and project management. Some important things to ask:
- Are you licensed, insured, and bonded?
- What kind of safety requirements and equipment do you have for your workers?
- What percent of the total cost do you require up front? (This should not be 100 percent. If it is, walk away. A balance of 20 to 30 percent should be left to pay upon completion.)
- What are your expectations for payment installments?
- How will you protect my home and yard as you work?
- What potential problems do you foresee? What will the process be to address those problems?
- Do you guarantee your work in addition to the manufacturer’s warranty?
- What is the timeline for the project?
- Will you provide a detailed contract with different elements itemized?
- Will you complete all aspects of the project, or do you hire subcontractors to finish the work?
FAQs
Metal roofs look like a simple option, but there are so many choices to make once you start investigating the possibilities. While you consider some of the more detailed decisions you’ll have to make, here are some questions homeowners frequently ask when considering installing this kind of roof.
Q. Is a metal roof cheaper than asphalt shingles?
At the outset, no—but in the long run, yes. Some sheet metal options can come close to the cost of asphalt shingles. Still, metal roofs require many more finish accessories than shingles, including ridge caps, fasteners, additional flashing, and other bits and pieces. Even a low-budget metal roof will likely be a little more expensive to install than an asphalt shingle roof, and the higher-grade material options are significantly more. However, the lifespan of a metal roof is easily double and maybe triple that of an asphalt roof.
Q. How long will my metal roof last?
On average, most will last 30 to 60 years. With good maintenance, some metal roofs can last as long as 100 years.
Q. Is a metal roof energy efficient?
Yes! Metal roofs are energy efficient in their production and function. Partially made of recycled materials and fully recyclable themselves, metal roof components have a smaller carbon footprint than other options. In addition, they reflect solar heat, keeping it cooler indoors during warmer weather, and insulate the home in colder weather as well, providing up to a 40 percent reduction in heating and cooling costs.
Sources: HomeAdvisor, Fixr, HomeGuide, Modernize