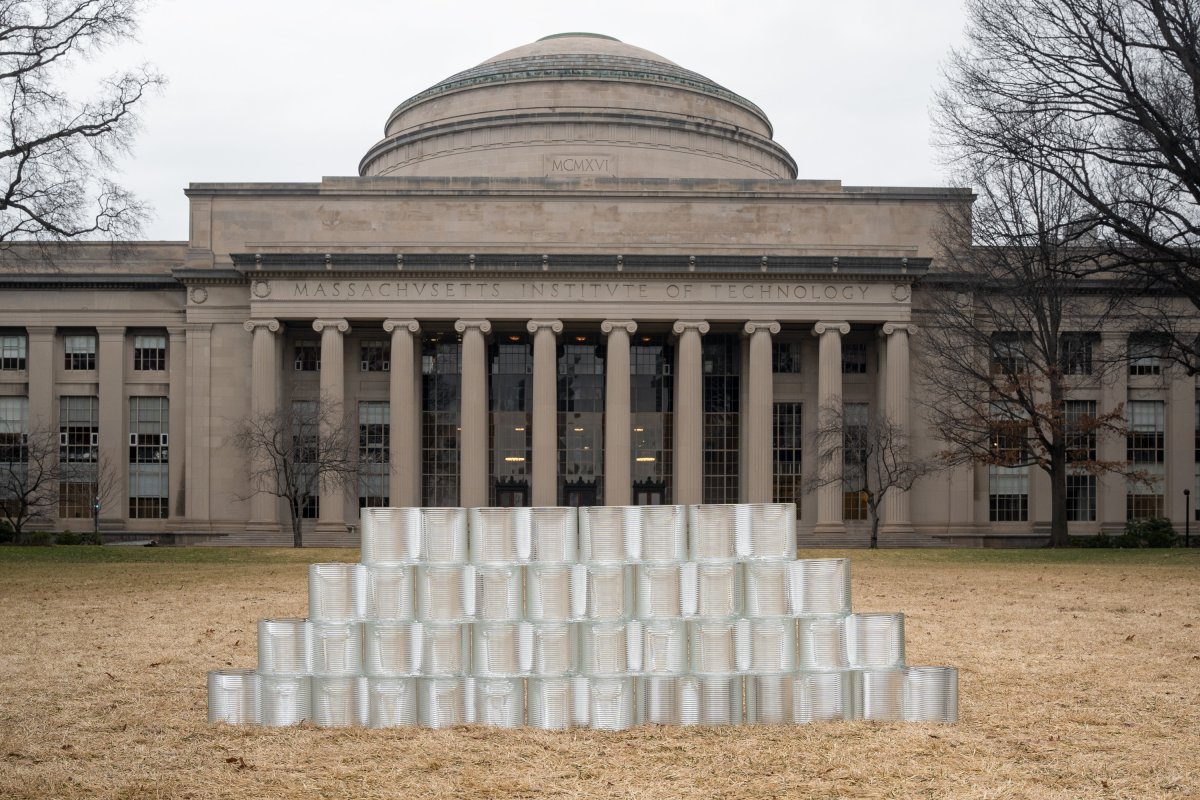
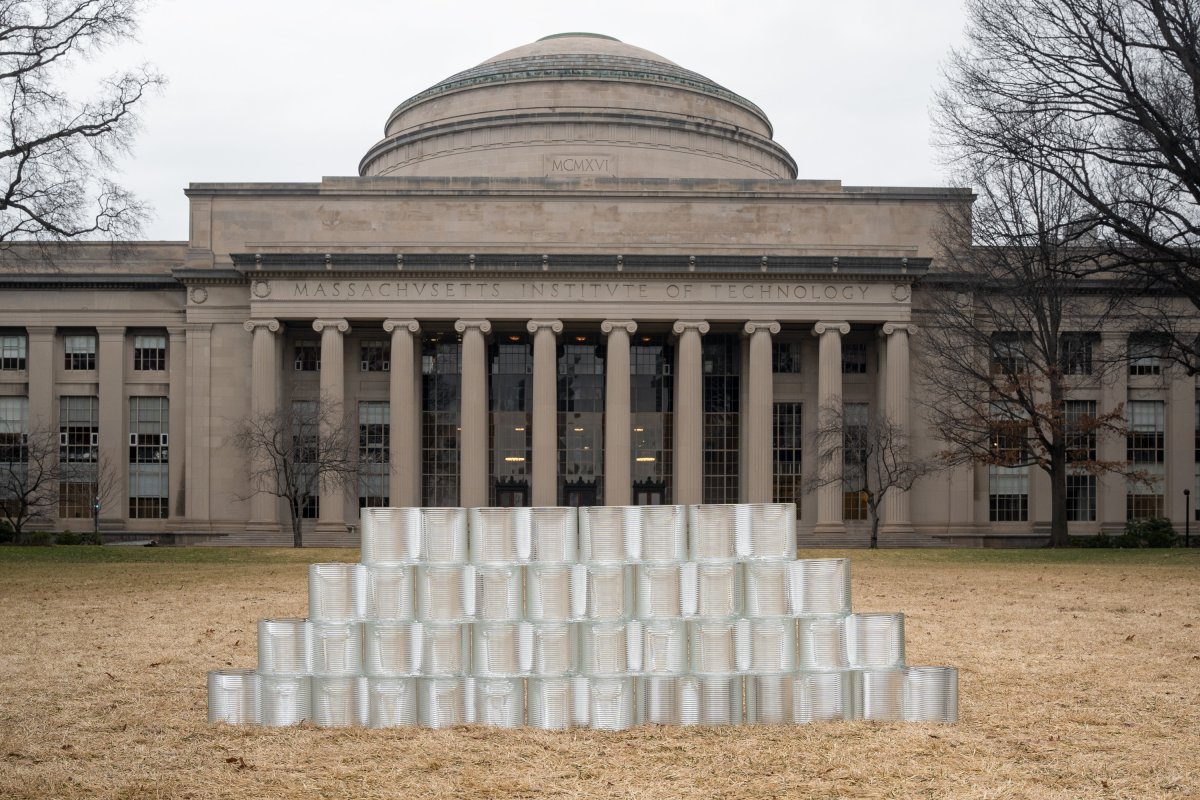
We may earn revenue from the products available on this page and participate in affiliate programs. Learn More ›
The future has arrived with 3D printing, and it’s not just for creating cute toys. Builders now are constructing fully livable homes with the power of this cutting-edge technology, both in the United States and abroad.
Although the 3D-printed housing market is in its infancy, it is expected to boom in the coming years due to advancements in technology, increased interest in sustainable construction practices, and a demand for affordable housing. The 3D-printed housing market was valued at $36.8 million in 2022 and is expected to grow to more than $1 billion by 2030, a growth rate of 61.5 percent during the forecast period (2023-2030).
While most 3D-printed homes are currently being constructed using concrete or plastic, engineers at the Massachusetts Institute of Technology (MIT) have just developed a way to 3D print construction blocks from recycled glass. This discovery could open up the 3D-printed housing market to new opportunities as demand increases.
What the Engineers Discovered
Kaitlyn Becker, assistant professor of mechanical engineering at MIT, and Michael Stern, a former MIT graduate student and researcher in both MIT’s Media Lab and Lincoln Laboratory, who is also the founder and director of 3D-printed glass manufacturer Evenline, have developed sturdy 3D-printed glass blocks to be used in building construction projects.
Detailing their glass brick design research and development in a study appearing in the journal Glass Structures and Engineering, the engineers created a new kind of reconfigurable masonry made from 3D-printed recycled glass. These interlocking, multilayered glass bricks have two round pegs and connect like LEGOs do. They can be linked together and stacked to build structures just like regular bricks. The engineers chose to design the bricks in a figure-8 shape, so they could be used to build curved walls.
The glass blocks are printed using Evenline’s custom 3D glass printing technology. It connects with a furnace to melt crushed glass bottles into a molten, printable material that the printer deposits in layered patterns. For their prototype, the team used soda-lime glass, which is common in glassblowing studios. An additional material is placed between the bricks to prevent scratches or cracks between glass surfaces.
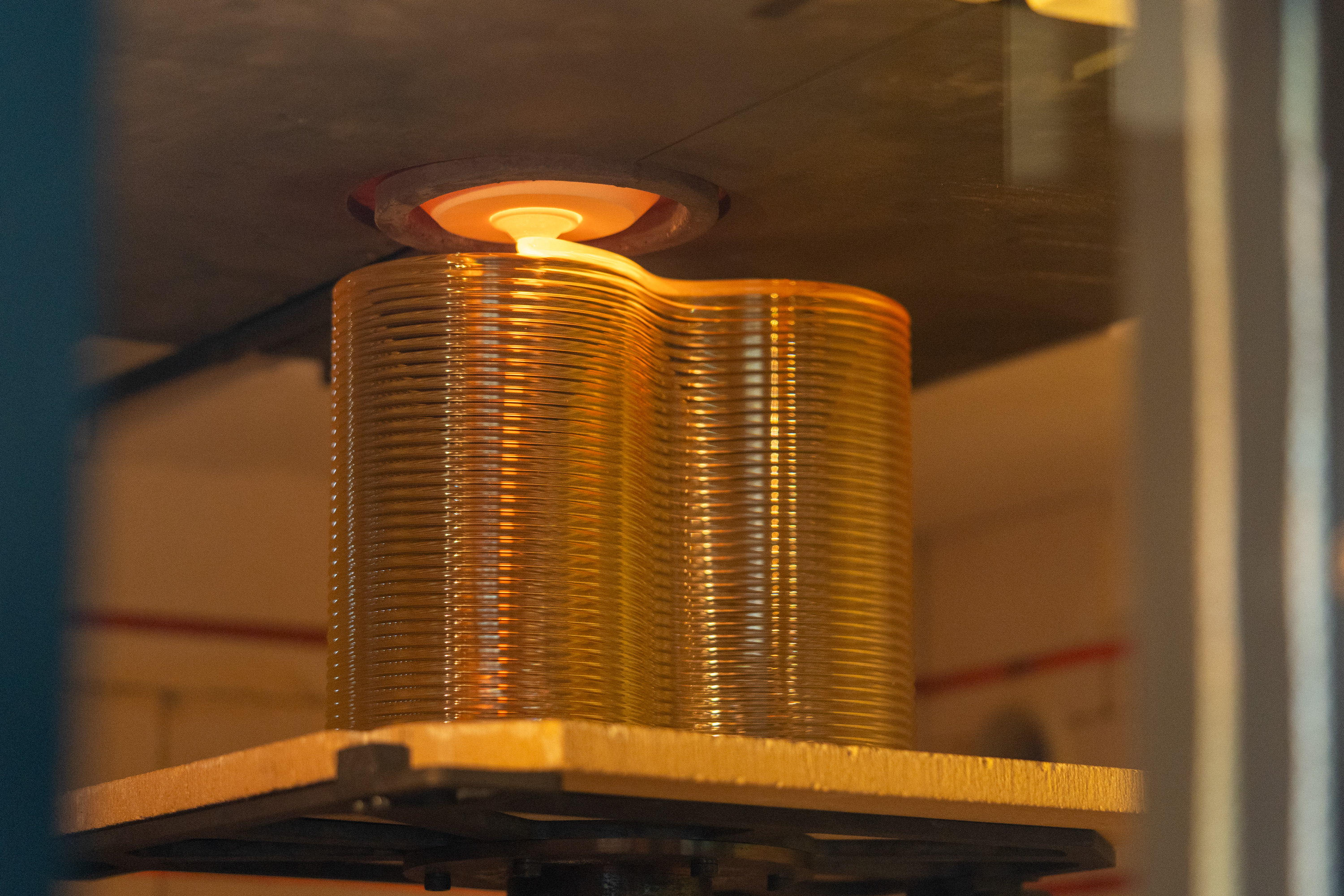
This Invention Tackles Environmental Challenges
The construction industry currently has a heavy environmental footprint. Manufacturing construction materials make up about 15 percent of global greenhouse gas emissions, and the construction and demolition industry sends more than 145 million tons of waste to landfills every year, according to the Environmental Protection Agency.
With these environmental challenges in mind, the MIT engineers wanted to find a more sustainable approach. They turned to circular construction, which aims to reuse and repurpose a building’s materials whenever possible. By creating glass blocks made from recycled glass that can be reused over and over again, they are minimizing the impact from manufacturing new materials. This, in turn, reduces the construction industry’s embodied carbon, which refers to the greenhouse gas emissions associated with all the processes throughout a building’s construction, from manufacturing to demolition.
The best part of glass is that it can be recycled endlessly, as long as it isn’t contaminated. That means these 3D-printed glass blocks can be disassembled at the end of a building’s lifetime and then repurposed many times over in new buildings. It can even be put back in the 3D printer to create completely new shapes.
How 3D Printing With Glass Compares to Concrete
The most common material used for 3D-printed houses is currently concrete. It is widely available, affordable, and able to be formed into complex shapes and structures necessary for construction projects.
The MIT team is aware of this, so they made sure to test their 3D-printed glass blocks to see how they compare to concrete. After testing the glass blocks using an industrial hydraulic press that squeezed the bricks until they began to fracture, they found that those made mostly from printed glass with separate interlocking features on the bottom were the strongest and held up to the highest amount of pressure. In fact, the layered blocks could withstand pressures similar to those that concrete blocks withstand.
These are promising results, and the team at MIT hopes that these glass blocks can soon be used as an alternative, or addition to, concrete and plastic to make 3D-printed houses.
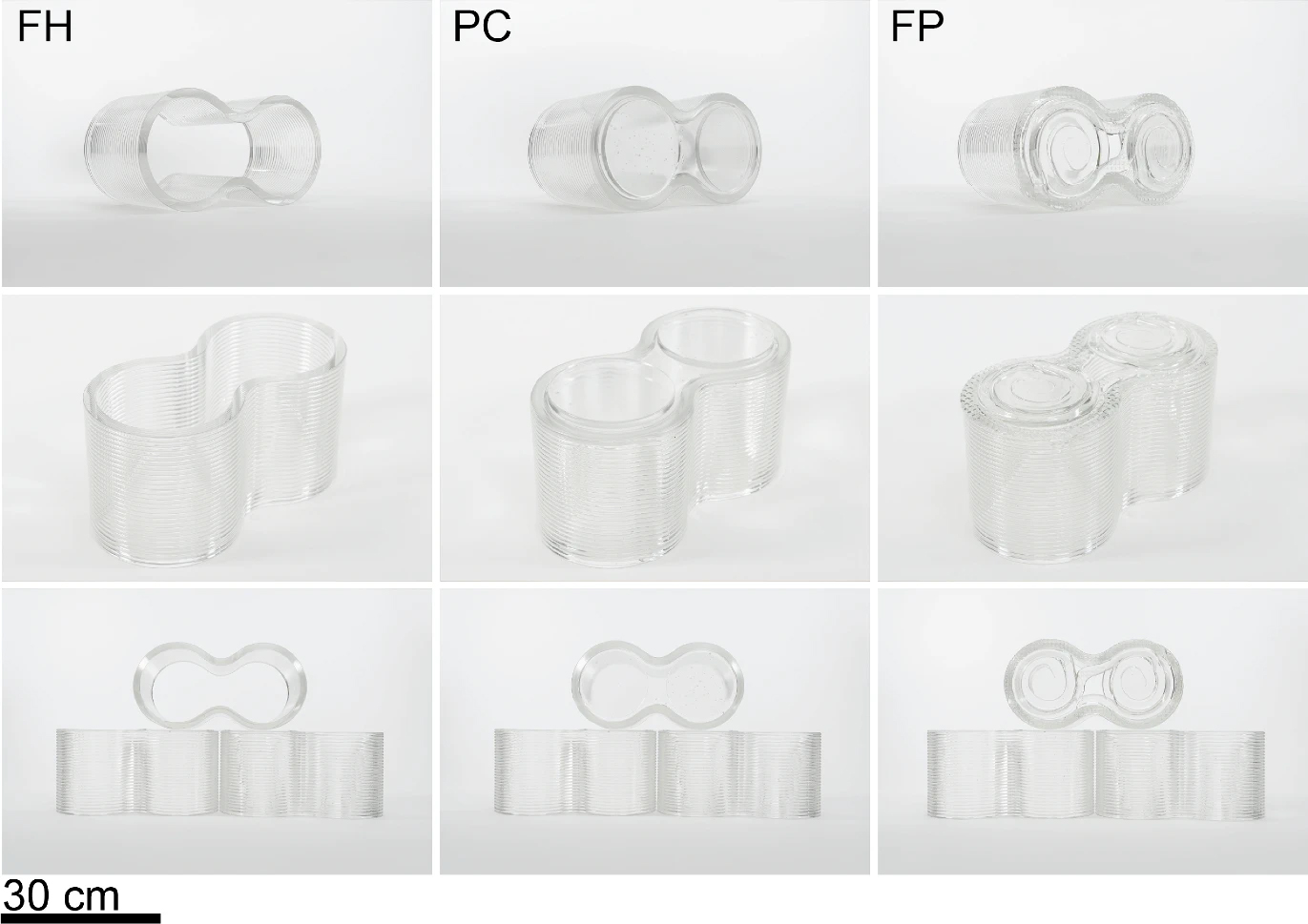
What the Future Holds
The MIT researchers plan to scale up their design to build larger structures, such as a pavilion. Between the new product they are bringing to the forefront and the potential for more demand and growth in the 3D-printed housing market, this is a sector to keep an eye on. We may soon see 3D-printed houses made from recycled glass bricks.
For now, you can find 3D-printed homes in a few locations. A housing development in Georgetown, Texas, has 100 3D-printed homes, and there are 10 houses so far in Austin. Habitat for Humanity helped build homes in Williamsburg, Virginia, and Tempe, Arizona, using the technology, and the company they partnered with plans to construct additional 3D-printed residences in Arkansas, California, Iowa, North Carolina, North Dakota, and Pennsylvania.