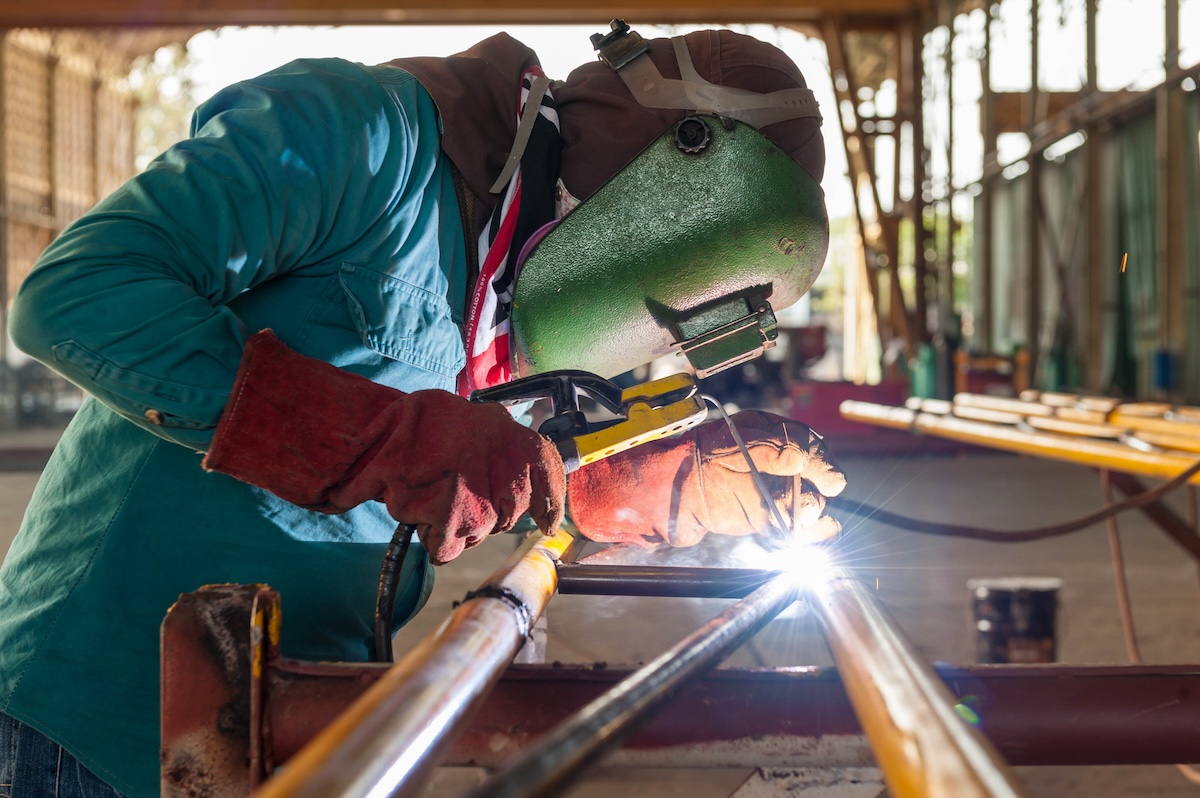
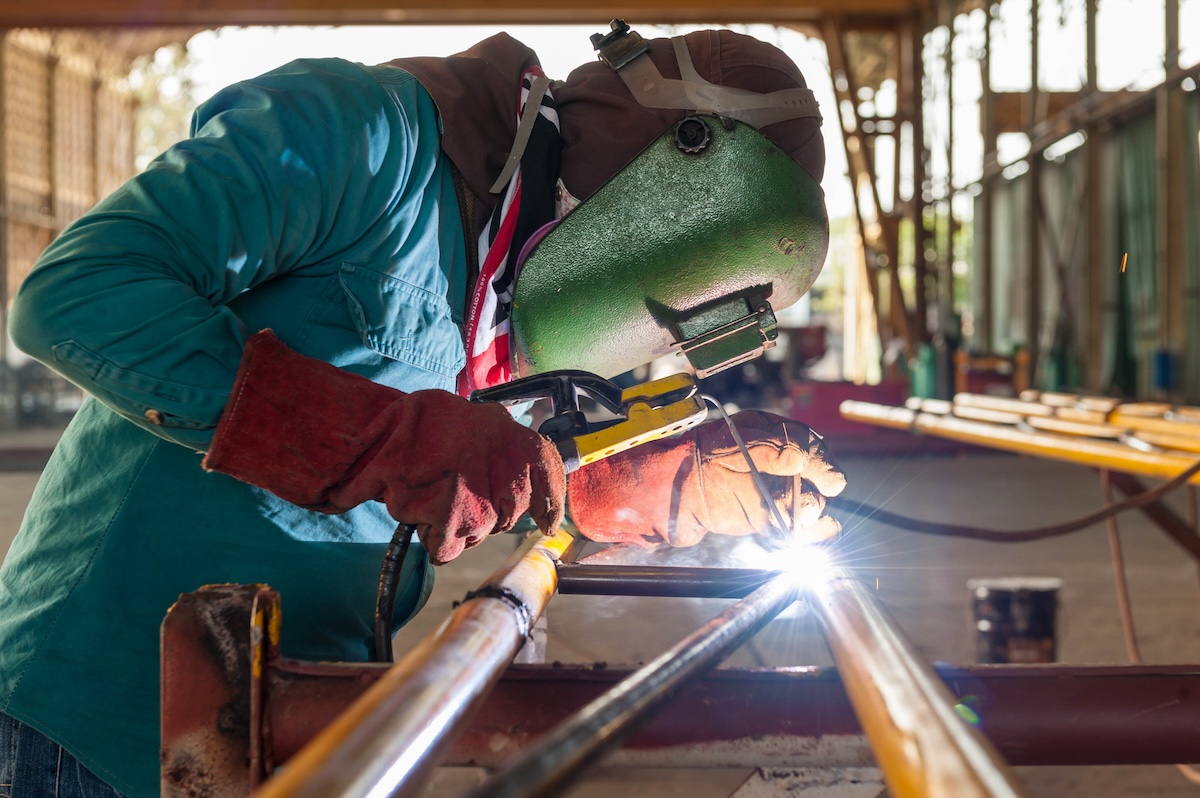
We may earn revenue from the products available on this page and participate in affiliate programs. Learn More ›
Stick welding, formally known as shielded metal arc welding, is the process of joining two pieces of metal by melting them using an electrical arc at the joint. Unlike other welding methods, stick welding can be performed horizontally, vertically, overhead and in windy weather, making it one of the more versatile welding methods. And since stick welding equipment is relatively compact and lightweight, it’s ideal for the jobsite or for a DIYer’s workshop where space is at a premium.
Stick welding also uses a simple setup that makes it a relatively easy method for beginner welders, and supplies and equipment are also more affordable with stick welding than with other welding methods. That said, safety is paramount with any type of welding, and stick welding is no exception. We tapped David Crosby, a general contractor and mechanic with more than 30 years of welding experience, for advice on how to stick weld. We’ll also review the equipment it requires, and offer stick welding tips.
Important Stick Welding Components
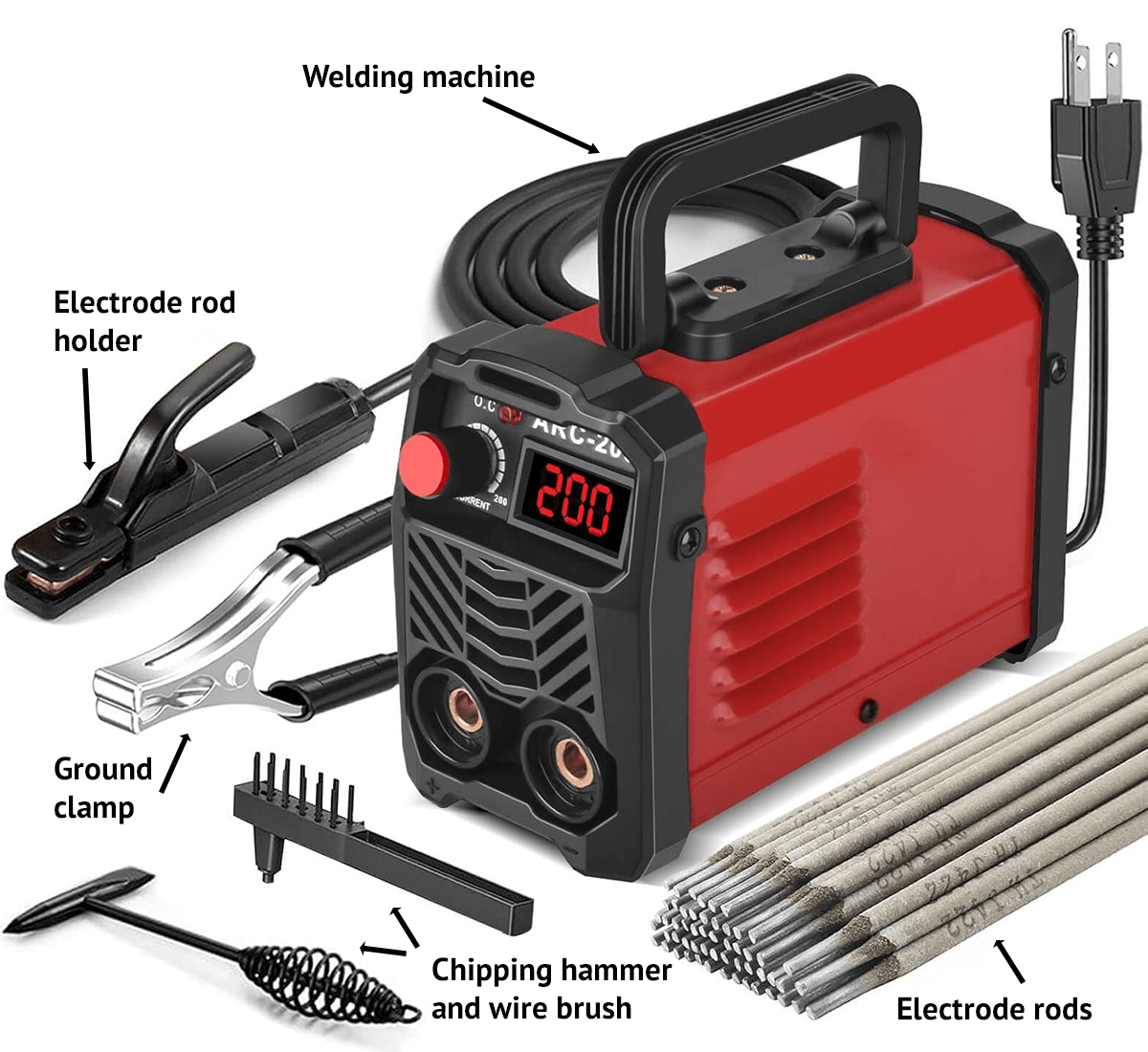
One of the reasons stick welding is so popular with DIYers is that the equipment it requires is relatively affordable and doesn’t take up much space. Here’s what you’ll need to get started:
- Electrode rod: The electrode rod, which is a wire that’s coated with a metal that is usually the same material that you’re welding together, has two purposes. It conducts the electrical current that creates the welding arc responsible for liquifying the metals and fusing them together. It also supplies the metal needed to create the weld.
- Welding machine: A welding machine for stick welding maintains a constant voltage regardless of the load that the welding machine is drawing, thereby allowing the user to maintain a consistent arc length while working. Most DIY stick welding machines are inverters, which are relatively compact, easy to pick up, and not tough to carry.
- Electrode rod holder: This device, which resembles a clamp with a handle, holds stick welding rods. Electrode rods are coated with flux, which releases a gas that protects the environment around the weld, preventing it from becoming contaminated by the surrounding air while it hardens.
- Ground clamp: This electrical cable consists of a clamp that attaches to the work piece and an end that connects to the welding machine, completing the circuit necessary to create a welding arc.
- Chipping hammer and wire brush: These tools are essential for removing the slag leftover from a weld.
Three Electrode Rod Types to Know
Unlike TIG and MIG welding, stick welding uses electrode rods to create the heat required for welding. These rods come in a variety of types and sizes to suit different applications and materials. Electrode rods are labeled with four-digit numbers. The first two numbers refer to the tensile strength, which is the amount of weight it can withstand after welding.
The third number refers to the position in which you can use the rod: horizontal, flat, vertical, or overhead.
- Rating of 1 is the most common. It means the rod is rated for any position.
- Rating of 2 is for flat and horizontal use.
- Rating of 3 is for flat use only.
The fourth number refers to the composition of the flux coating around the rod. A lower number sets more quickly, creating more identifiable weld marks, while a higher number is softer material that creates a flatter and smoother weld.
Below are three of the most commonly used electrode rod types:
1. E6010
An E6010 welding rod is notable for creating a deep cutting arc. This makes it ideal for thicker metals or for penetrating metal that’s coated in rust or dirt. An E6010 rod is also one of the harder electrode rods to work with, requiring more experience from the operator to prevent them from digging too deep into the metal.
2. E6013
A good general purpose electrode, E6013 works in a variety of welding applications. They leave a clean, professional looking weld and are easy to work with. “The E6013 is normally the go-to electrode for beginners and all-around use,” says Crosby. “It works on any polarity in any position, the slag is easy to remove, the penetration is mild, so it’s easier to not blow through thin sections, and it’s easier to learn how to control heat and travel speed.”
3. E7018
E7018 electrodes are typically the choice of professional welders. They produce a clean arc that limits spattering, allowing the operator to create a strong, smooth bead that requires little post welding clean-up.
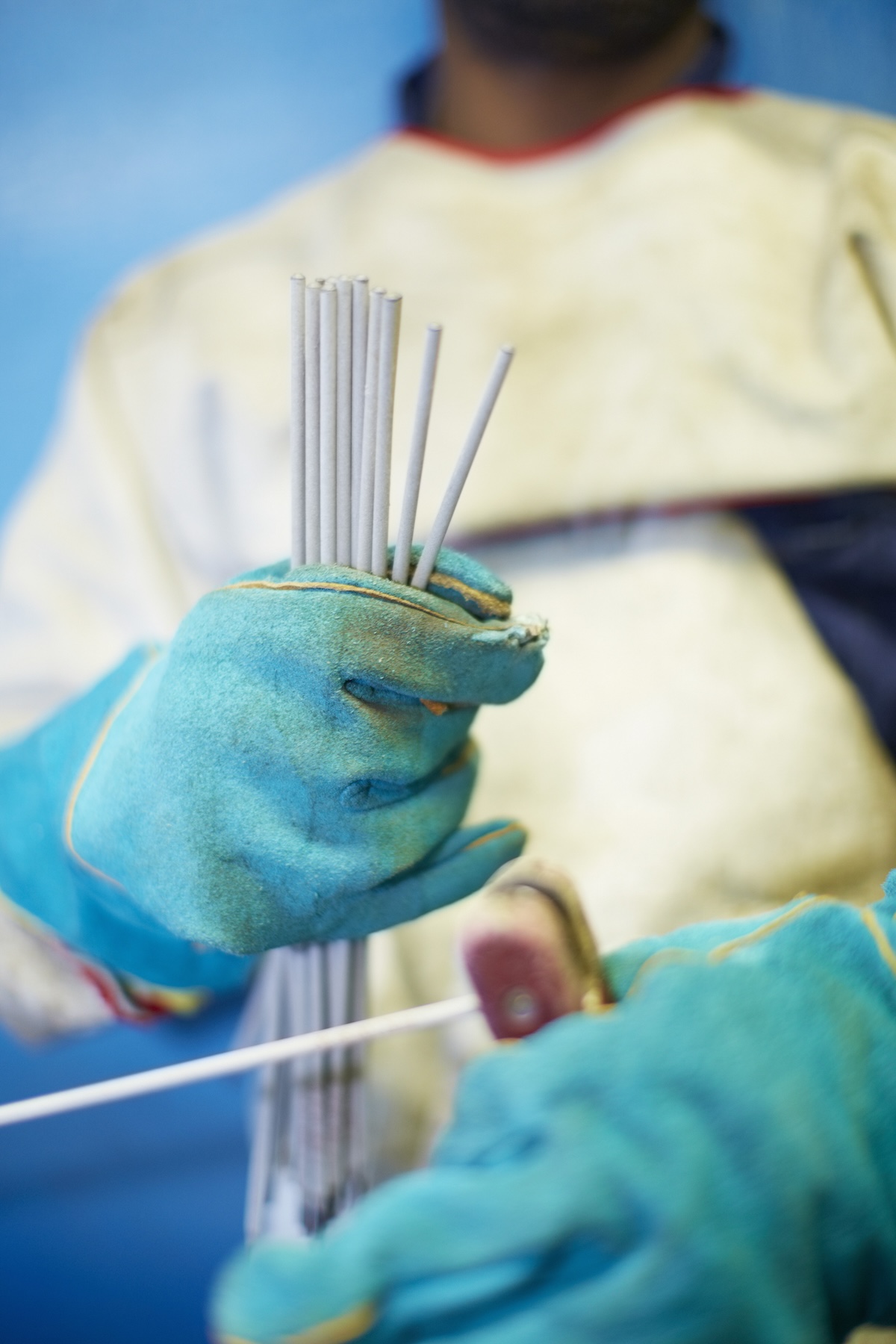
Important Stick Welding Safety Tips
Given that stick welding can reach temperatures approaching 7,000 degrees Fahrenheit while creating dangerous UV radiation, taking safety precautions and employing good practices when stick welding is crucial. “You’re dealing with very high temperatures, and in most cases, powerful electric currents,” says Crosby. With this in mind, he recommends the following safety precautions:
- PPE. Wearing the proper Personal Protective Equipment (PPE) is crucial. This includes a welding helmet (we suggest an auto darkening hood, like this highly rated option available at Amazon, that’s easier to work with for beginners), a fire-resistant welding apron or jacket, leather boots, a respirator, and welding gloves.
- Fire extinguisher. Don’t weld near any flammable or combustible materials and keep a fire extinguisher nearby.
- Dry surfaces. With stick welding, you’re working with electricity, so be sure to work on dry surfaces and be mindful of the welding leads. “Do not, do not, have your body in between the welding leads,” Crosby says. Doing so puts your body in the pathway for electricity, which can result in electrocution.
Initial Setup and Calibration
Start by choosing an electrode that suits the types of job and material (see above). Plug in the welding machine and set the amperage based on the electrode type and thickness. Calibration settings are typically on the electrode label. You can also find a stick welding amperage chart online.
Next, set up the polarity of the welding machine to match the electrode rod. The rod’s polarity will be listed on its box.
For an AC/DC+ electrode, connect the welding machine’s ground clamp to the negative port on the welding machine and attach the clamp end to the workpiece, then attach the electrode holder to the positive side. FOR AC/DC-, connect the ground clamp to the positive side and the clamp to the negative mount.
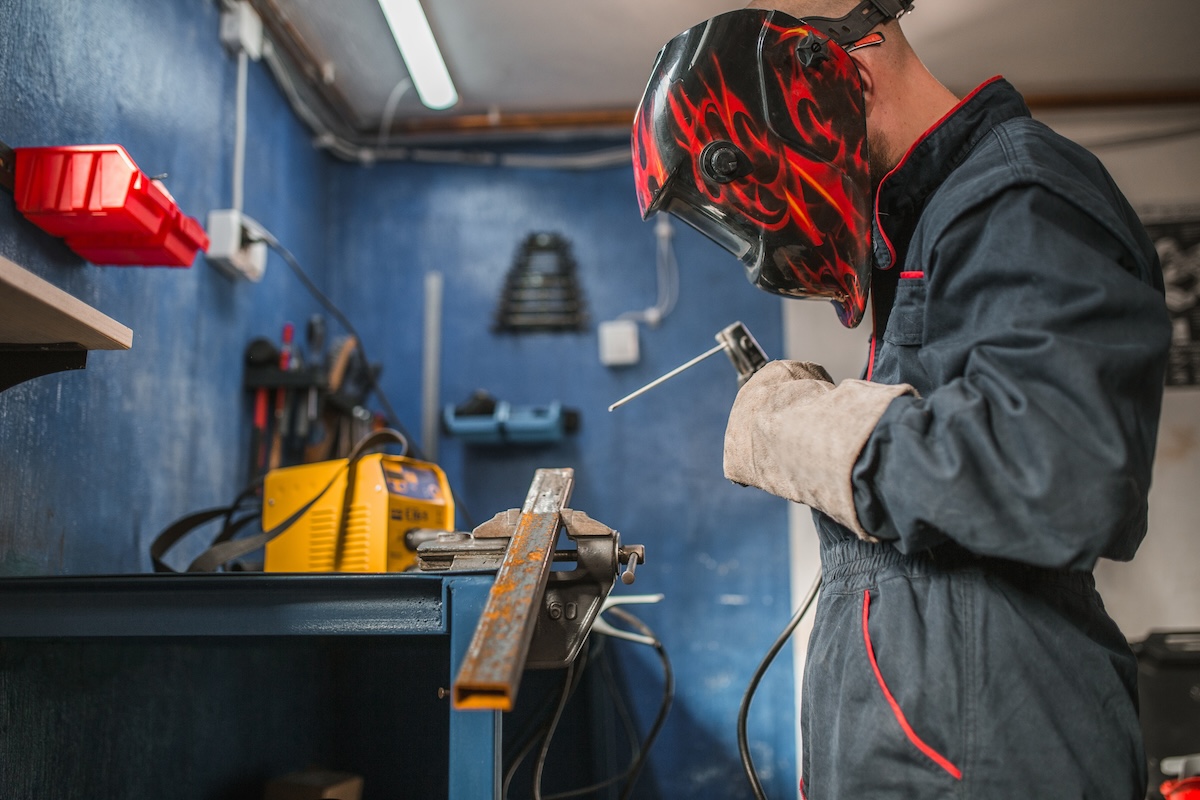
How to Stick Weld
Stick welding methods all follow the same general guidelines, with some variances depending on the type of joint you’re welding.
STEP 1: Prep the surface.
One benefit of stick welding is that it eliminates the need to clean rust and dirt off metal before beginning the weld because of the flux coating on the electrodes that it uses. That being said, having a clean starting area is key to establishing an arc, especially for beginners. Crosby recommends using an angle grinder with a flap wheel. You can also use a wire brush to remove any grime or rust from your starting area. The key here is to have both the clamp and rod contacting bare metal.
STEP 2: Strike an arc.
Attach the electrode holder to the end of the rod. Make sure the clamp only contacts bare metal and not the flux to ensure a clean connection.
Check the end of the rod and make sure the tip is not coated over with flux. Touch the end of the electrode to the workpiece in a quick motion that’s similar to striking a match, then pull it slightly away from the surface. This will create a spark that ionizes the air, allowing you to establish a welding arc. “It should sound just like eggs frying in bacon grease when you have it right,” Crosby says.
If you don’t pull the tip off the metal fast enough, the electrode may stick to the metal, in which case you’ll need to make a quick twisting motion to release it. If you pull the tip too far from the surface of the workpiece, you’ll lose the arc and need to start over again.
Striking an arc is perhaps the most challenging part of stick welding for beginners. Crosby says the best way to become proficient is through practice. “It doesn’t matter if you didn’t finish high school or just completed your post-doc work, it might take some time and practice to acquire that skill,” he says. “Get some scrap steel, clean it, and burn some rod.”
STEP 3: Start the weld.
Hold the rod so that it’s at a 10- to 15-degree angle from the workpiece and drag the rod along the weld line, moving in a straight line. Don’t push the rod along the weld, as doing so could strap slag in the weld pool, contaminating the weld.
STEP 4: Maintain even distance and speed.
To get a good weld, you’ll also want to maintain a consistent arc, which requires you to maintain a distance from the material that’s no greater than the diameter of the rod. This can be a challenge given that the rod will shorten as it melts. Use your off-hand to help prop up and steady the dominant hand that’s holding the rod in order to maintain proper control and distance.
Speed is also key. Go too slow and you’ll leave a wide weld or even overheat the material and melt completely through it. Move too fast and you won’t penetrate deeply enough into the material to create a strong connection. Your goal is to produce a weld that’s about twice the width of the diameter of the rod.
Practice making welding lines over a piece of scrap material to get a feel for what travel speed produces the proper weld width before moving forward with your weld.
STEP 5: Clean the weld.
Once the weld is complete, there’s likely to be some slag left behind. Clean up the weld by removing the excess bits of slag with the chipping hammer and wire brush.
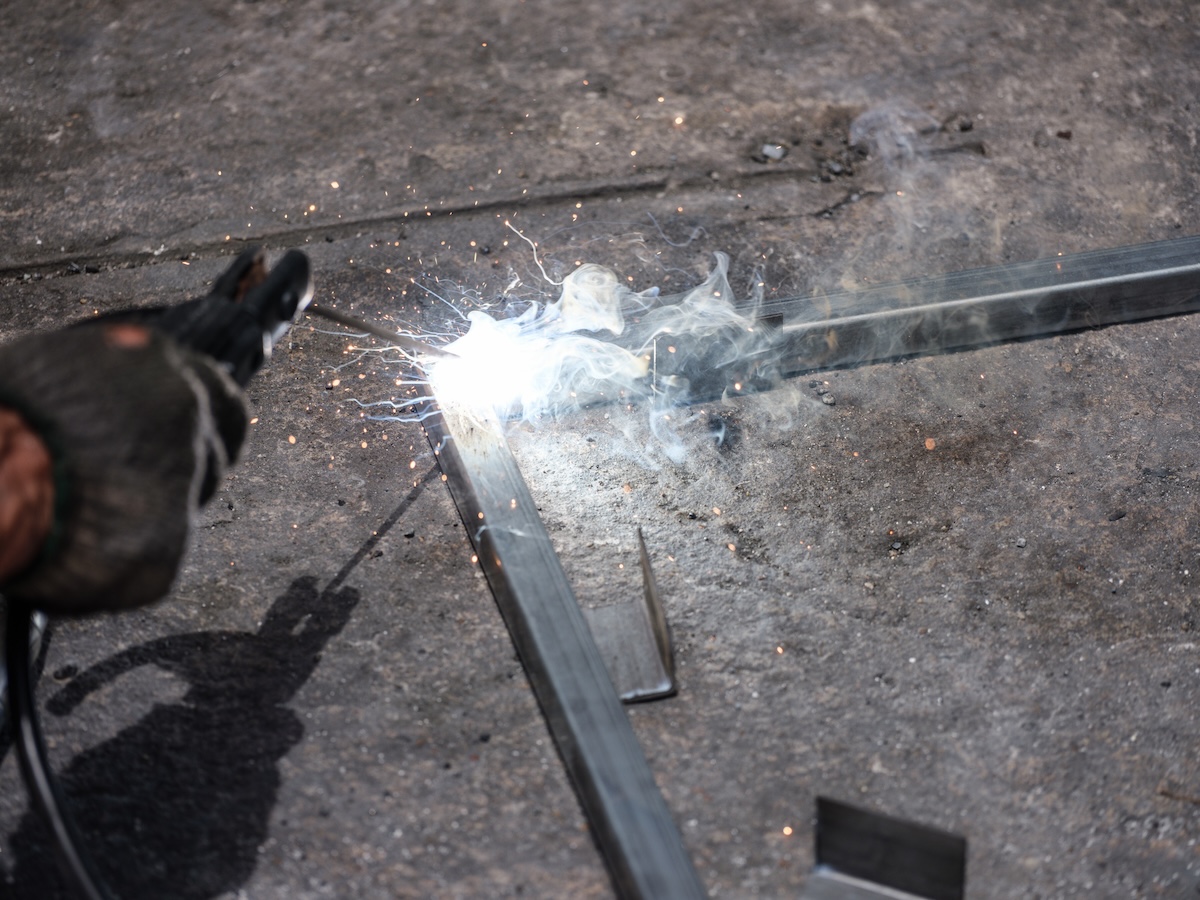
Stick Weld Joint Types
While experts recommend holding the welding rod at a 10- to 15-degree angle that points forward, the angle at which you hold the rod in relation to the workpiece will vary depending on the type of weld.
Butt Joint
A butt joint is when two pieces of material are butted up against each other. When making a butt weld, the electrode should be positioned so that it’s at a 90-degree angle in relation to the workpieces.
T-Joint
A T-joint weld is when you’re joining two materials to form a T-shaped joint. When executing a T-weld, point the electrode so that it’s at a 45-degree angle in relation to both pieces.
Lap Weld
A lap weld is when you join two pieces of metal that are overlapping each other. As with a T-joint weld, you’ll want to hold the electrode so that it’s at a 45-degree angle to the work pieces when executing the weld.
Final Thoughts
Stick welding is a simple and affordable method for welding, which is why it’s such a popular option for beginners. However, there’s an art to learning how to weld well. Your first efforts at stick welding are likely to result in choppy weld lines that vary from thick to thin. Don’t get frustrated. As with most things, practice makes perfect. “Read everything you can find on the subject, practice, practice, practice, and be safe,” Crosby says.